摘要
本文研究了航空发动机涡轮叶片的检测与维修技术,分析了叶片失效模式及检测维修关键技术。新型材料的使用和结构设计的改进提升了叶片性能,但也增加了检测和维修难度。文章介绍了低周疲劳断裂等失效模式及相应的检修技术,并讨论了热喷涂等维修方法。这些技术提高了叶片性能,延长了使用寿命。随着高性能发动机的发展,精确检测和先进维修技术将成为航空发动机领域的重要发展方向。
正文
涡轮叶片是航空发动机的重要组成部分,具有温度高、负荷大、结构复杂等特点,检测与维修质量与工作的耐久性和使用寿命密切相关。本文进行航空发动机叶片的检测与维修研究,分析了航空发动机叶片失效模式,总结了航空发动机叶片失效检测技术与维修技术。通过以上研究表明:先进的检修技术在航空发动机叶片维修中得到广泛的运用,极大地改善了其运行的可靠性和降低了使用寿命成本。
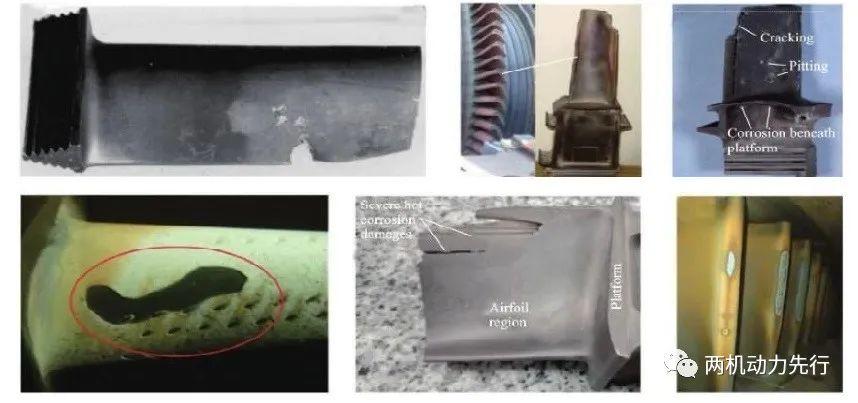
在涡轮叶片设计中,经常使用较高的新型材质,并通过改进结构和加工技术,减少工作余量,从而达到改善发动机推重比。涡轮叶片是一种气动力的翼型它能在叶片的整个长度上实现等值做功,从而保证气流在叶根和叶尖之间有一个旋转角度,在叶尖上的旋转角度大于叶根处。在涡轮盘上安装涡轮转子叶片非常重要的,“枞树形”榫头是现代燃气轮机的转子,它经过精密的加工设计,确保了所有的凸缘都能均匀地承受负载。在涡轮机静止状态下,叶片在齿槽处有一个切向运动,而在涡轮机旋转时,由于离心的作用,使叶根拉紧于圆盘。叶轮材料是确保涡轮机性能和可靠性的重要因素,早期使用的是变形高温合金,采用锻压工艺制造。随着发动机设计和精铸工艺的不断进步,涡轮叶片由变形合金向中空、多晶向单晶转变,叶片的耐热性得到了极大改善。镍基单晶超合金因其优异的高温蠕变特性而被广泛应用于航空发动机热端零件的生产。因此,对涡轮叶片的检测与维修进行深入研究,对于改善发动机工作的安全性、准确地评价叶片的损伤形态和破坏程度具有十分重要的意义。 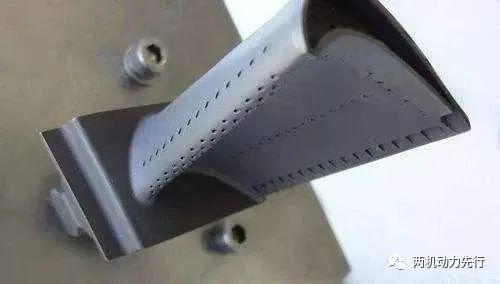
1 航空发动机叶片失效模式
1.1 叶片低周疲劳断裂失效
在实际工作中,转子叶片的低周疲劳断裂通常是不易发生的,而在下列三个条件下,则会发生低周疲劳断裂,图1为叶片断裂示意图。
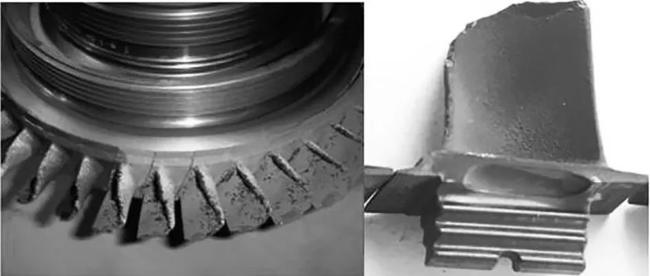
图1 叶片断裂
(1)虽然在危险断面上的工作应力比材料的屈服强度要小,但是在危险断面处有很大的局部区域缺陷。在这一区域,由于存在缺陷,导致附近更大面积超出了材料的屈服强度,导致大量塑性变形,从而导致了叶片的低周疲劳断裂。(2)由于设计上的考虑不周,叶片在危险断面上的工作应力接近或超出了材料的屈服强度,而在危险部位有多余的缺陷时,叶片会发生低周疲劳断裂。 (3)在叶片发生颤振、共振、超温等异常状况时,其危险断面的总应力值大于其屈服强度,从而导致叶片的低周疲劳断裂。低周疲劳断裂主要是由设计原因引起的,大部分发生于叶根周围,在典型的低周断口处没有明显疲劳弧线。 1.2 叶片扭转共振疲劳断裂失效
高周疲劳断裂是指在桨叶扭谐振下发生的断裂,有以下的代表性特点: (2)在叶片的疲劳断裂处可以看到明显的疲劳曲线,但是疲劳曲线很细。 (3)断裂通常从叶背开始,扩展到叶盆,疲劳区占了断裂面的主要区域。 叶片扭振疲劳裂纹产生的原因主要有两个:一是产生扭振谐振,二是叶片表面有广泛的锈蚀现象,或者受到外力冲击。 1.3 叶片高温疲劳与热损伤疲劳断裂失效
涡轮转子叶片工作于高温环境,经受着温度的变化和应力的交替作用,从而导致了叶片的蠕变和疲劳破坏(见图2)。叶片发生高温疲劳断裂,需要满足下列三个条件: 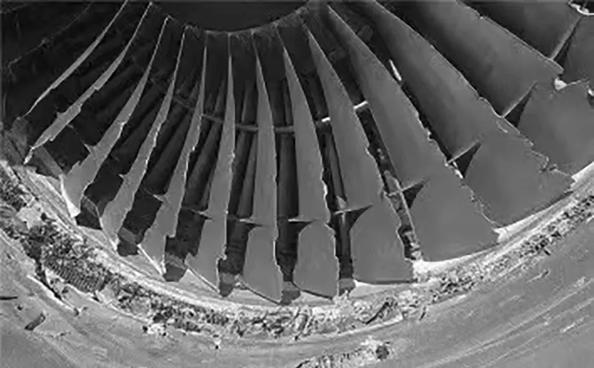
图2 叶片疲劳破坏
(1)在叶片的疲劳断口处,主要表现为沿晶断裂特点。 (2)在叶片断裂部位,其温度高于材料的极限蠕变温度; (3)在叶片的疲劳断裂部位,仅能经受方波形的离心拉伸应力,超出了此温度下的蠕变极限或疲劳极限。 通常,转子叶片在高温下发生疲劳断裂是极少见的,但在实际使用中,由于转子的热破坏而产生的疲劳断裂是比较普遍的。在发动机运行中,因不正常工作状态下的短暂超温,造成部件过热或过烧的情况,称之为过热损伤。在高温下,叶片叶片容易出现疲劳裂纹。高温损伤导致的疲劳断裂具有以下几个主要特点: (1)断裂位置一般位于叶片的最高温度区域,与叶片轴线相垂直。 (2)断裂起源于源区的进口边沿,其截面为深色,氧化程度较高,延伸段的剖面比较平整,颜色没有源区的深。 2 航空发动机叶片失效检修技术
2.1 机上孔探检测
机上孔探检测是通过在发动机透平箱内的一个探头,通过孔探仪对涡轮叶片进行目视检测。该技术无需拆装发动机,直接在飞行器上完成,既方便又快速。孔探检测能较好地检测出涡轮叶片的烧熔、腐蚀和脱块,可以帮助了解、掌握涡轮的技术和健康状况,从而对涡轮叶片进行全面检查,确保发动机的正常运行。图3 为探孔检测。
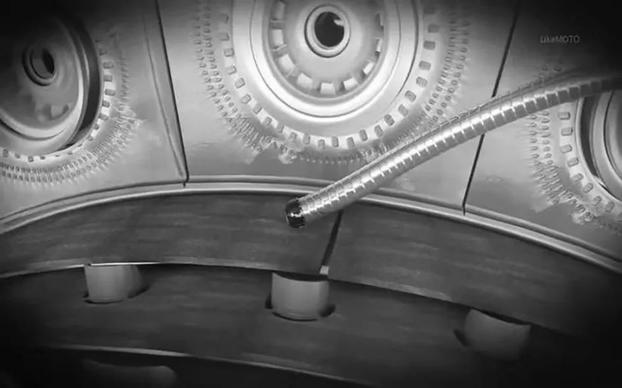
图3 探孔检测
2.2 修理车间检测前的预清洗处理
在涡轮叶片的表面,附着着燃烧后的沉积物质、涂层和高温氧化腐蚀形成的热蚀层。积碳会导致叶片的壁厚增大,从而导致原来的气流通路发生变化,从而降低涡轮效率;而热腐蚀则使叶片的力学性能下降;而且由于积碳叶的存在,对叶片表面的损害进行了遮蔽,使得检测变得困难。所以在对叶片进行监控和维修之前,必须对其进行积炭清理。
2.3 叶片完整性检测
以往采用“硬”测量仪如角规、卡尺等对航空发动机的叶身径进行检测,这种方法简单,但容易受到人工干扰,存在准确度不高、检测速度慢等缺陷。随后,基于坐标测量机,编写了用于微机自动控制的应用程序,开发了用于叶身几何尺寸的测量系统,通过对叶身进行自动检测,与标准叶型进行对比,自动给出误差测试结果,以判定叶片的可用程度及所需的维修方法。虽然不同厂家的座标测量仪在特定技术上存在差异,但是具有如下共性:自动化水平高,探测快速,一般1分钟即可完成一个叶片的探测,具有很好的扩展能力,通过修改一个标准的叶型数据库即可实现对各种类型叶片的检测。图4为完整性检测。
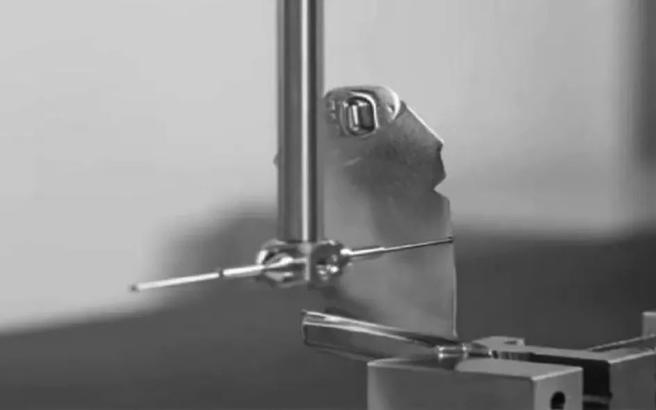
图4 完整性检测
3 航空发动机叶片维修
3.1 热喷涂技术
热喷涂技术是将纤维或粉状物质烧至融化状态,进一步雾化,然后再将其沉淀于待喷涂的部件或基质上。
(1)耐磨涂层
航空发动机零部件中广泛采用的是钴基、镍基、碳化钨基等耐磨涂层,以降低航空发动机运行时的振动、滑动、碰撞、摩擦等摩擦造成的摩擦,提高性能和使用寿命。
(2)耐热涂层
为了增加推力,现代航空发动机需要将涡轮前的温度提高到最大。这样,涡轮叶片的工作温度就会随之升高。尽管采用了耐热材质,但还是难以达到使用的要求。试验结果表明,在涡轮叶片表面涂耐热涂层,可以改善零件的耐热性,避免零件的变形、开裂。
(3)可磨耗涂层
在现代航空发动机中,涡轮是由多个水平的静叶构成的机壳和一个固定于圆盘上的转子叶片构成。为了提高发动机的效能,静子和转子的两个部件间的间距要尽可能地减小,这个间隙包含转子叶尖和固定外环的“叶尖间隙”,以及每每级转子-机箱的“级间间隙”。为了减小间隙过大造成的空气泄露,理论上要求这些空隙尽量为零,因为生产部件的实际误差和安装误差很难实现;此外,在高温、高转速的情况下,轮盘也会发生纵向移动,使叶片沿径向“增长”。由于工件的绕曲变形、热胀冷缩等原因,采用喷涂磨损涂料,使其具有最小的意识间隙,也就是在叶片与叶片顶部附近的表面上喷涂各种涂料;在转动的部件与其发生摩擦时,涂层会产生牺牲磨损,从而将间隙减至最小。图5为热喷涂技术。
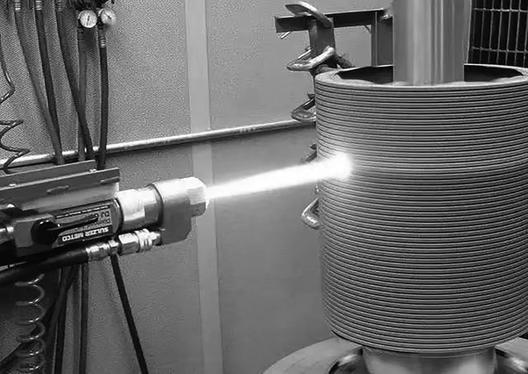
图5 热喷涂技术
3.2 喷丸强化
喷丸强化技术是利用高速度弹丸冲击工件的表面,在工件表面产生残留的压应力,并在一定程度上形成了一种强化材料,以提高产品的疲劳强度,降低材料的应力腐蚀性能。图6为喷丸强化后的也叶片。
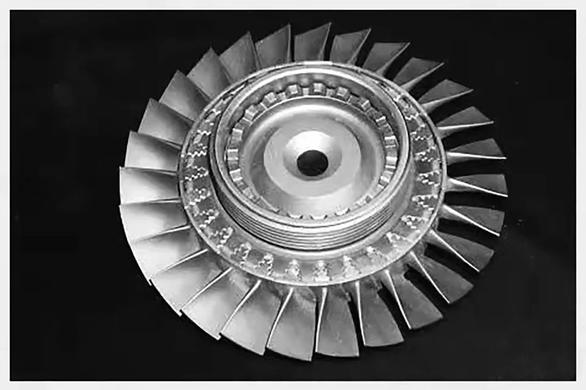
图6 喷丸强化后的也叶片
干式喷丸强化技术是利用离心力作用,在工件表面形成一种具有一定厚度的表面强化层。干式喷丸技术虽然设备简单、效率高,但是在批量生产过程中仍存在着粉尘污染、噪音大、弹丸消耗大等问题。 水喷丸与干喷丸具有相同的增强机理,不同之处在于,它通过快速移动的液态颗粒来代替弹丸,从而降低了干干喷丸过程中的粉尘对环境的影响,从而提高工作环境。 美国3M公司研制了一种新型的喷丸增强工艺,它的强化方法就是用带着弹丸的旋板,在高速转动下,对金属表面进行连续的打击,形成一种表面强化层。与喷丸强化相比,具有设备简单、使用方便、效率高、经济耐用等优点。旋板强化是指当高速弹丸冲击到叶片上时,叶片的表面会快速膨胀,使其在某一深度处产生塑性变形。变形层厚度与弹体冲击强度及工件材料的力学性能有关,一般可达到0.12~0.75mm。通过调整喷丸工艺,可以获得适当的变形层厚度,在喷丸作用下,在叶片表面发生塑性变形时,邻近次表面也会发生变形。但与表面相比,次表面的变形量要小,在没有到达屈服点的情况下,仍处于弹性形变阶段,所以表面和下层之间的非均匀塑化是不均匀的,能引起喷涂后的材料产生残留应力变化。试验结果表面,喷丸后表面有残留的压缩应力,而在某一深度下,次表面处出现拉伸应力,表面的残余压缩应力是次表面的几倍,这种残余应力分布非常有利于改善抗疲劳强度和抗腐蚀能力。因此,喷丸强化技术对于延长产品的使用寿命,改善产品的质量起着十分重要的作用。 3.3 涂层修复
在航空发动机上,很多先进的涡轮叶片都采用了涂料技术,以改善其抗氧化、抗腐蚀、耐磨等特性;但是,由于叶片在使用中会出现不同程度的损伤,所以在叶片维修时必须对其进行修补,通常是将原来的涂层剥离,然后再涂上一层新的涂料。 4 结论
由于航空发动机叶片工作环境恶劣,合金材料价格昂贵,因此,对其进行力学性能的检测与维修越来越引起航空发动机领域的关注。多年实践表面,先进的检修技术在航空发动机叶片维修中得到了广泛的运用,极大地改善了其运行的可靠性和降低了使用寿命成本。随着新型高性能发动机的研制生产,将会采用先进的叶片材料和制造技术,从而大大提高了涡轮叶片的成本。因此,对于航空发动机来说,采用涡轮叶片的精确检测和先进维修技术应用非常有前景。 免责声明: 本文来源于《内燃机与配件》