面向通用化模块化开发的电驱NVH性能集成
摘要:为应对产品通用化对整车性能集成带来的挑战,文章研究讨论了在通用化模块化开发策略下,电驱系统噪声、振动与声振粗糙度(NVH)性能控制及电动车整车 NVH 性能集成应对方案。电驱系统通用化为电动汽车开发普遍采用的平台化策略,文章重点从驱动系统本体和传递路径两方面研究讨论了对应的 NVH 开发策略。从脉冲宽度调制(PWM)控制方式、齿轮精度、电磁结构和壳体结构等方面,尽量降低驱动系统本体的振动噪声;同时利用模态解耦、布置、声学包、密封、隔振和智能声场修饰技术等多种技术,基于“传递路径”的优化、声声传递路径和声振传递路径来实现整车 NVH 性能的差异化要求。在整车开发过程中,实施通用化模块化战略,能够缩短开发周期、降低开发费用、提升可靠性和产品质量。与此同时,还可以减少采购成本、制造设施投入、精简制造流程、提升售后服务便利度。因此,产品平台化和通用化成为提升公司竞争力的重要手段,这已经是全球汽车行业的普遍共识[1]。通用化工作固然可以带来巨大的效益,但也给整车性能集成带来一系列的挑战。对于整车性能来说,不同车型往往针对不同的潜在客户,性能属性需要有针对性的差异化开发,而通用化需求则意味着对应的模块和零部件具备同样的实际性能。整车性能集成在项目前期完成二级开发计划和关键开发关键路径后,就会基于企划目标完成整车技术目标设定,并进一步分解到子系统和零部件的技术要求。从整车角度来看,任何单一零部件都有可能出现性能不足或性能过设计的情况。在通用化策略推进过程中,通用化零部件为了适配高端车型的需求,更容易出现性能过设计的情况。整车性能集成需要充分考虑通用化零部件的实际性能,完善整车技术目标体系,以达成合理的整车性能,满足整车技术开发目标[2-4]。本文讨论了通用化模块化整车开发策略下电驱本体噪声、振动与声振粗糙度(Noise, Vibration,Harshness, NVH)性能控制技术及电动车整车NVH 性能集成应对方案,并探讨了模块化通用化的整车性能集成设计。为提升通用化率,必须在项目前期完成车型平台开发策略,并制定相应的通用化模块化开发策略[5]。其中,重点是下车身及底盘系统的开发,需要提前充分考虑多个车型的设计需求和制造需求。一般性总体策略是最大限度保持关键力传递路径不变,并通过车身带宽架构件来调节车辆在X、Y、Z 方向的变化,以实现平台拓展和车型演化。前舱系统集成了动总、底盘、热管理、内外饰等多个关键系统,且对于碰撞安全、结构强度等整车性能都有非常重要的影响,所以同平台车型前舱的力传递主路径和结构设计都会保持不变,而防撞梁、减震塔以及外造型件等部分零件根据不同车型需求进行适配,如图 1 所示。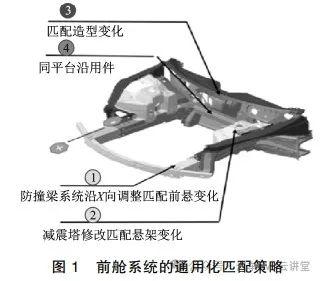
为了提高通用化率,一般根据最高配置车型进行匹配设计开发,同时做好其他车型的设计保护,特别是动总系统、轮胎系统等。前地板系统受座椅布置、电动车动力电池布置、轴距尺寸变化等因素综合影响,一般保持主体车身座椅横梁不变,座椅横梁上增加支架的方式实现高度变化;在与电池匹配的 Y 方向,各平台车型保持一致,X 向调整长度匹配电池 X 向变化。通过改变前地板后端区域来满足不同车型的轴距变化,与此同时,通过调整门槛外板的变化来调整车身宽度,如图 2 所示。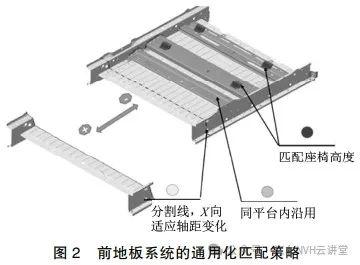
后地板因受到后排座椅布置,后悬架形式变化、后驱动类型变化、后悬变化等因素的影响,相应的平台变化较多,但原则上关键力传递路径和纵梁形式保持不变。为了充分保护后纵梁主体的沿用性,后纵梁可分为两段,前端在车型变化时不受影响;而后端包括后防撞梁、外造型件等部分零件,以适应不同车型变化进行调整,如图 3所示。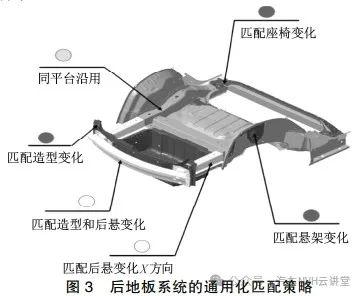
在车体架构和底盘架构的通用化匹配策略制定和开发过程中,需同步进行动力总成、电子电器等系列零件的通用化和模块化策略制定,以及通用化零部件的设计开发和性能集成。通用化零部件性能设计,是整车性能集成设计的起始重要参考点,各属性部门从开始就要参与定义通用化零部件的设计,确认通用化零件是否满足各个属性的整车开发要求[6]。在整车性能开发路径中,通用化零部件由于需要适配多个车型平台,其性能目标及设计优化需特别关注。通常,潜在的通用化零部件众多,牵涉到动力总成、电子电器、底盘、车身、内外饰等系统内的众多零部件。其中,驱动系统通用化是汽车行业普遍采用的通用化策略,对于电动汽车,电驱动系统就是典型的通用化零部件。电驱动系统在运行过程中,会带来车内外噪声和整车抖动等一系列 NVH 问题。按照“源-路径-响应”的 NVH 开发思路,首先需要从电驱系统源头尽量加以控制。同样,通用化模块化开发一般也是按高配性能的设计要求进行设计保护。目前,国内的电动汽车普遍采用高功率密度、低扭矩波动和小物理尺寸的永磁同步电机。从NVH 表现来说,电机 NVH 性能问题主要包含脉冲宽度调制(Pulse Width Modulation, PWM)解调噪声、齿轮阶次噪声、电磁阶次噪声等。永磁同步电机一般采用 PWM 系统供电,由PWM 系统将电池的直流电转换成与电机转速匹配的交流电,故存在以 PWM 开关频率为基频的载波频率所引起的调制解调噪声。如图 4 所示,在随着电机转速变化过程中,载波频率不变,但载波信号的包络频率随转速变化,导致解调后的噪声频率变化且往两边发散,主观感知较差。一般都是提高载波频率,将噪声转移到人耳不敏感的高频区域内(8 000 Hz 以上);或者采用随机 PWM开关策略来降低开关频率的幅值并将电机电磁噪声改变为限带白噪声。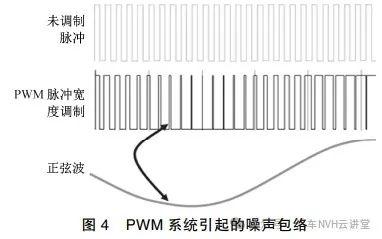
齿轮噪声主要由齿轮啮合、轴承啮合、花键啮合、装配偏心等因素引起的传递误差造成,可通过齿轮修形和磨齿工艺进行优化。电磁噪声是由电机本身的结构特性、气隙磁场、电磁力波造成,可通过优化定转子的齿槽配合、增大气隙等因素进行优化。从声辐射角度来看,电驱系统本体辐射出来的声能量是壳体振动扰动壳体表面的空气层所辐射出来的。但是与电驱系统振动能量相比,由于空气密度远低于电驱系统密度,所以表面空气层所包含的振动能量非常低。与此同时,在非壳体模态频率范围,辐射出来的声能量与表面空气层中振动能量相比也非常小。这是由于壳体结构表面的弯曲波波速远小于空气声速(吻合频率以下),空气振动能量无法有效转换成声能量辐射。但是电机尺寸有限,在壳体模态频率范围,弯曲波会转换为驻波,从而将表面的空气层振动能量全部转换为声能量辐射出来。所以需要尽可能提高电机壳体模态,降低本体的声辐射。在各阶壳体振动模态中,需特别关注具备高声辐射效率的模态。声辐射效率是指可以辐射到远场的声能量与结构表面空气层所具有的振动能量之比。而高辐射效率的模态,是指结构表面的声辐射效率较高的辐射模态,一般复杂振动结构的声辐射模态通过数值法对辐射阻抗矩阵进行特征值分解获得。另外,在很多情况下,NVH 抱怨往往是产品功能性偏差的一种表现,电驱系统内部任何损伤或异常运转也都会表现 NVH 问题。在通用化策略下,为实现差异化的整车性能开发目标,需要从其他开发手段上充分考虑差异,进行合理的性能匹配和设计优化。因为电驱系统的通用化意味着具备相同的 NVH 本体水平,但是,各车型平台可以结合其他具体设计,利用模态解耦、布置、声学包、密封、隔振和智能声场修饰技术等多方面来优化电驱系统带来的车内NVH 表现,实现不同的整车性能要求。激励源往乘客舱传递噪声的途径,按照传递路径区分,可分为空气声和结构声。其中,结构声是激励源的振动通过车身悬置激励车身产生的车内噪声,空气声是激励源的辐射声通过车身透射到车内的车内噪声。对于同一激励源产生的辐射噪声 Qi(ω)和激励力 Fi(ω),可以通过控制声声传递路径 HQi(ω)和声振传递路径 Hfi(ω)来优化车内噪声水平,满足整车开发要求,即

整体模态分布图通常以整车车身为中心,将各主要激励源与整车车身模态、主要零部件和局部钣金的模态互相错开,避免共振和拍频问题。例如:整车蠕行工况下,动力总成主要阶次频率需要避开整车弯扭频率,以避免共振问题;与此同时,电机主要阶次频率(包括电机阶次、减速器齿轮阶次)也需要避开(建议 15 Hz 以上),以避免拍频问题。动力总成的布置需要从结构布置和空间布置两方面进行考虑。由于动力总成尺寸较大,实际可调范围不大。一般还是通过被动手段来提升车内性能。结构布置上,主要提升动力总成悬置安装点的动刚度、降低车身噪声传递函数(Noise TransferFunction, NTF)和车身振动传递函数(VibrationTransfer Function, VTF)。空间布置上,临近的硬边界(声学上)会反射动力总成辐射噪声,形成同相声源。同相声源会大幅提高电驱动系统的声辐射效率,并且形成强指向的辐射特性。所以,一般在临近的反射面上布置吸声材料,降低辐射效率。电驱动系统的悬置系统是降低电驱动系统激励力往车身传递的最重要手段。悬置系统有着重量支撑、位移约束和隔振保护等多重作用,故需具备足够的抗扭限位能力、合理的刚体模态和解耦率。与此同时,为提高隔振率,悬置支架模态要足够高,并充分考量过渡段和非线性段的刚度和隔振设计。与传统内燃机的悬置不同,电驱系统 NVH 问题主要是中高频(500 Hz~2 000 Hz)的齿轮副啮合噪声和电磁噪声,故悬置隔振设计要特别关注中频段的隔振设计。此时,激励频率远高于悬置系统的刚体模态频率,隔振优化可以考虑采用尼龙悬置等设计来增加阻尼,虽然会一定程度上降低悬置系统刚体模态频率附近的隔振效果,但是可以大幅增加宽范围的中高频隔振效果。为进一步提高悬置隔振能力,降低路径上的振动传递,可采用软连接副车架或者橡胶螺栓形成二级隔振结构来提高中高频隔振效果。声学包是降低车内中高频噪声的重要手段,对于电驱动系统,首先可以采用电驱总成整体声学包裹方案,从源头降低电驱系统辐射出来的声能量。与此同时,还可以通过前围隔声、前舱吸声、乘客舱吸声等一系列声学包配置来降低电驱动系统噪声对车内的影响。图 6 为典型的用于声学包性能分析的统计能量分析(Statistical EnergyAnalysis, SEA)模型。其中,最重要的是前围声学包的隔声设计。目 前 , 常 用 的 前 围 声 学 包 中 乙 烯 醋 酸 乙烯酯(Ethylene Vinyl Acetate, EVA)重层,由于真空吸附制造工艺问题,存在拉薄现象,会导致重层真实面密度低于设计状态,且不均匀,最薄区域往往只有设计状态的一半左右,存在隔声短板效应。一般可以利用注射成型(Ceramic Injection Moulding, CIM)工艺设计成可变密度的 EVA 重层来优化前围隔声特性,弥补隔声不足区域。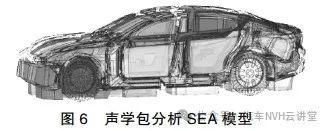
整车密封是 NVH 开发的重要基础,密封性能的不足会导致隔声性能的不足。项目开发前期,可以在模型中通过最速路径方法查找车辆的孔洞和钣金间隙。图 7 为钣金泄露路径查找分析的示意图。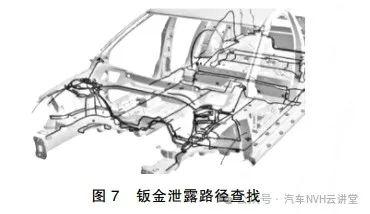
整车密封不足表现为车内外之间存在多个孔隙,包括功能孔、定位孔以及钣金制造间隙等。由于这类间隙往往远小于声波尺寸,声波通过小孔时,由于板面收缩和管壁摩擦带来的声阻抗,声能穿透能力减弱。声波尺寸相对于间隙越小,声能穿透能力越强。所以,从隔声角度出发,需尽量减小孔隙面积,缩小孔隙尺寸。在既定的车内声场环境下,还可以借助声场修饰技术来改善车内响应,如图 8 所示。首先获取车辆运行状态(车速、踏板位置等),匹配次级通道估计,通过车载娱乐系统来修饰车内声场。可借助掩蔽效应降低电机啸叫声,增加客户期望的声响应,改善声品质。它的意义不仅在于可降低客户可感知的噪声,更可以借助艺术家的设计,打造品牌的声场特征,与品牌整体定位相适应。1—4:扬声器。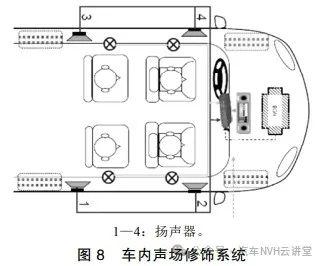
基于通用化模块化开发背景下,本文讨论了电驱系统 NVH 开发技术及电动车整车 NVH 性能集成应对方案,并进一步探讨了通用化模块化策略下的零部件性能设计和整车性能集成。(1)通用化模块化策略要求尽量适配多个车型平台,同时需要满足差异化的性能要求。所以,从 NVH 角度,“激励源”一般采用通用化策略,而“传递路径”是实现差异化性能要求的主要手段。其中,电驱系统通用化是电动汽车普遍采用的通用化策略。(2)电驱系统应按照其所搭载车型平台的高配置性能要求进行设计优化,从 PWM 控制方式、齿轮精度、电磁结构和壳体结构等方面尽可能降低驱动系统本体的振动噪声。(3)利用模态解耦、布置、声学包、密封、隔振和智能声场修饰技术等多方面来改变电驱系统往车内传递的声声传递路径和声振传递路径,实现不同的整车 NVH 性能要求。【免责声明】本文转载自网络
著作权归作者所有,欢迎分享,未经许可,不得转载
首次发布时间:2024-03-10
最近编辑:1月前