损伤的涡轮叶片修复对航空发动机的检修及延寿具有重要意义。本文综述了某镍基铸造高温合金涡轮工作叶片修复技术的研究进展,重点介绍了叶尖部位自适应机械加工的修复方法,深入阐述了试验加工过程与验证结果,并对涡轮叶片修复技术的发展前景进行了展望。
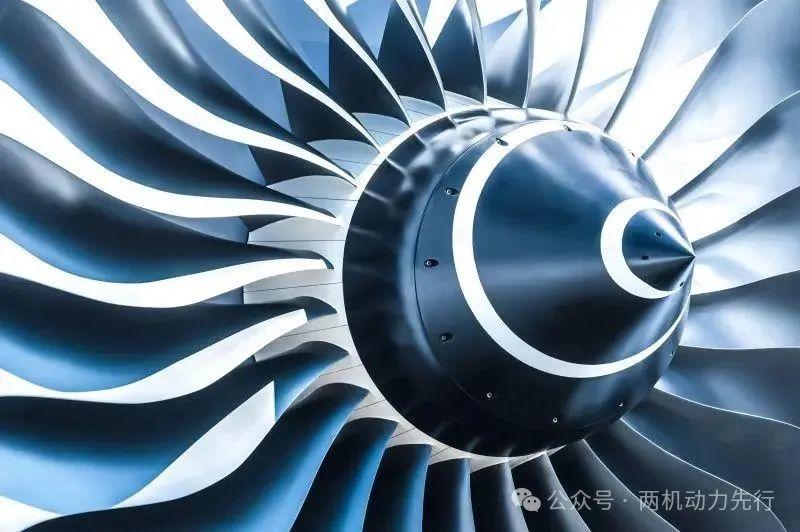
航空发动机是飞机的动力核心,在航发的各组成部件中,涡轮工作叶片的功能使命及其工作特点决定了它在航空发动机中是受力恶劣、承载最大的转动部件之一,这也造成涡轮工作叶片常见失效破损。其中,裂纹失效出现的概率最高,其危害也最大,主要为离心力叠加弯曲应力引起的疲劳裂纹、振动环境引起的颤振疲劳裂纹以及有环境介质引起的腐蚀损伤导致的高温疲劳裂纹。现阶段,为了降低发动机使用成本,对损伤涡轮工作叶片的再制造修复有着极其重大的意义。 20世纪70年代末,美、英等国就在军/民用喷气发动机叶片部件修复技术的研究中投入了巨额资金。至今,损伤叶片的再制造修复技术仍被国外垄断,如MTU、Chromalloy等国外著名发动机制造和维修企业大都采用激光熔覆结合自适应磨抛加工,叶片修复后有良好的精度和性能。而国内航空公司和发动机制造厂由于缺少叶片部件的修复技术,或是直接按叶片报废处理或是依赖国外技术资源进行维修,价格昂贵,进度很慢,颇受制约与限制。 在涡轮叶片修复的关键技术中,自适应加工技术作为实现破损边界光滑搭接与修复区域高精度成形的有效手段,得到了众多研究人员的重视。英国TTL公司通过接触式的测量方法,获取叶片截面线的信息并利用测得的截面线轮廓信息通过沿Z向偏置完成叶尖磨损区域的模型重构,并生成去除熔覆层的加工代码。英国Delcam公司针对涡轮叶片叶尖修复提出在机测量完成模型重构方式,通过在机测量减少了定位误差累积问题;利用接触式测量方式获取熔覆层附近的两个横截面数据,计算出该直纹叶片叶尖的磨损的待修复几何模型,从而进行磨削加工完成了整个修复过程。丁华鹏基于灰色系统理论,预测了损伤区域叶型中弧线和厚度,进而重构完整的叶片模型,然后通过布尔求差得到修复缺损模型,从而获得了一定的修复效果。HouF等提出了一种叶片叶身自适应的修复方法,包括焊接表面建模以及目标修复曲面的优化建模,并最后用仿 真 证明该修复方法的有效性。Zhang X等提出了一种发动机叶片自动化损伤区域修复方案,直接通过材料熔覆成型,与传统的修复工艺方法相比,有一定的创新性,但针对复杂型面涡轮叶片存在一定难度。 上述研究表明,航空发动机叶片修复是国内外航空领域研究的一个热点。在修复的机加工领域,重点是实现修复区域与非破损区域之间的光滑搭接,以及修复后的高精度成形。因此,本文在上述修复研究的基础上,以破损涡轮工作叶片为例,开展叶尖损伤修复的自适应加工技术应用研究,保证修复后叶片的加工区域与非加工区域能实现光滑过渡搭接,且整体修复型面满足修复叶片的最终公差要求。
1 叶片叶尖损伤修复工艺性分析
图1为典型涡轮工作叶片叶尖裂纹缺陷,由此提出一种航空发动机涡轮工作叶片叶尖损伤再制造修复方法,建立一套叶尖损伤部位去除—熔焊堆积焊料(如图2所示)—叶片点云获取—叶片数字化模型重建—叶片自适应加工的再制造修复解决方案,实现叶片几何尺寸精度的自适应修复与性能恢复。修复后的叶片质量与性能满足设计要求,可用于修理现场实时修复,为实现航空发动机破损构件批量修复加工提供了一种有效解决方法。
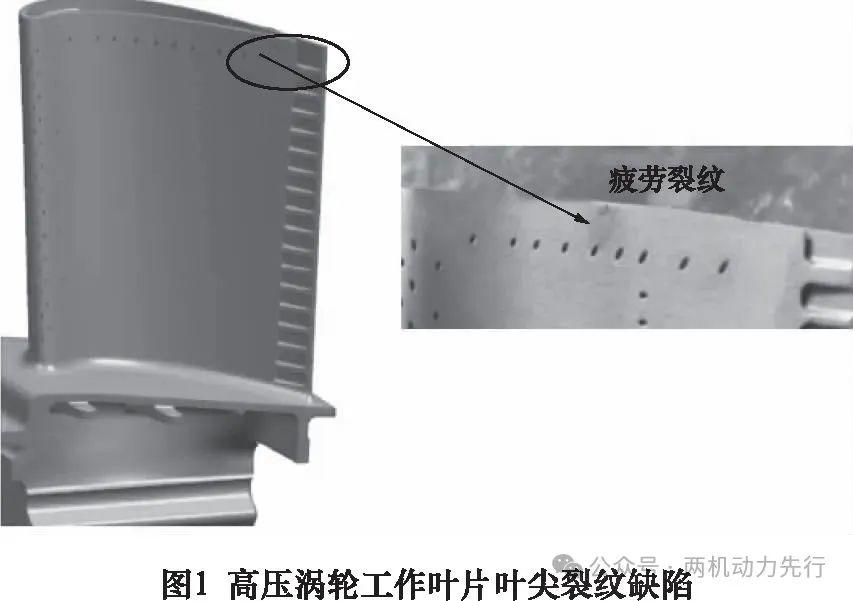
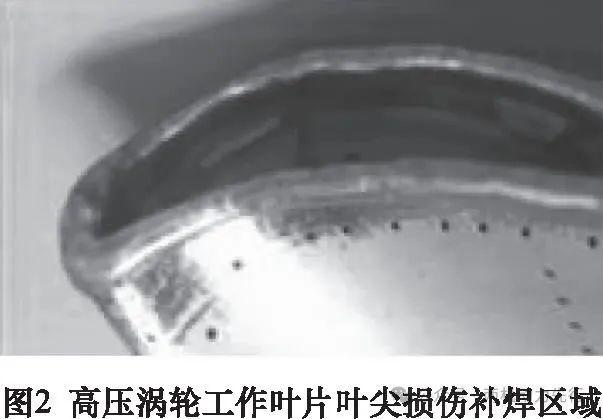
1.1 工艺难点分析
由于铸造精度的问题,叶片成品与理论设计模型存在个体差异。叶片轮廓尺寸在新品状态形成,在使用一个工作周期后,又会产生不同程度的变形及缺陷,由于被加工对象个性化,如若按照设计图理论尺寸修复加工,将破坏原有叶片的形状精度,如若每件加工时都需按照CAD模型重新生成一套加工代码,则大大影响零件整个加工周期。 叶尖部位结构复杂,叶尖下部2~3 mm处有凸台和盖板,后缘尾缝最狭窄处宽度仅为0.5 mm。叶片是内腔结构,叶身型面分布多排气膜孔,切屑易进入内腔及气膜孔,难于清理。
1.2 主要技术要求
(1)叶尖修复加工后,内、外曲面轮廓形状符合设计图,与原基体叶型连接光滑过渡。 (2)保证叶尖后缘尾缝处沿叶型最小壁厚0.41 mm,其余部位沿叶型最小壁厚0.51 mm(如图3所示)。 (6)荧光检查修复区域,无裂纹、夹杂等,按荧光检测标准、验收标准执行。 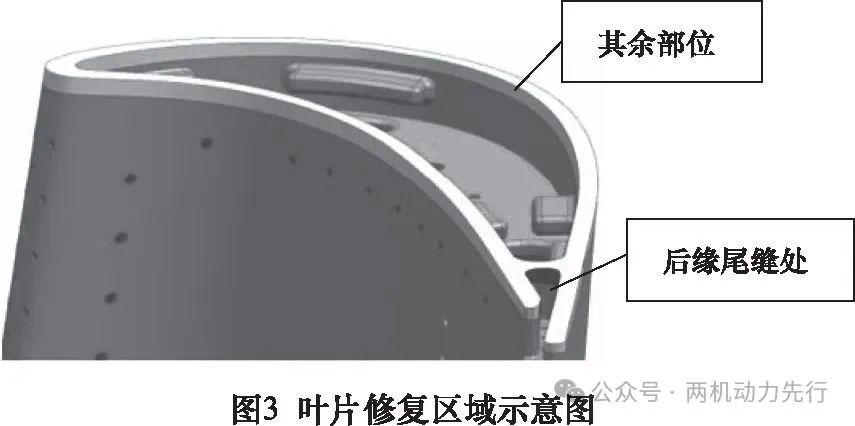
2 叶片叶尖损伤修复自适应加工技术
自适应技术是为了满足某些特殊领域的需求而发展起来的一项新的综合集成应用技术,它在多种加工技术领域都有应用。自适应加工技术是保证产品最终外型尺寸的闭环过程控制系统。它的运行机理是通过在线的测量加工区域,工件装夹位置等,了解零件的余量分布及弹性变形,计算出目标曲面,透过对理论模型和路径接触点进行比对,重新自动生成运动轨迹,确保加工出的零件与设计相符。自适应过程中产生的数据文件可以反传回质量控制管理系统,生产过程中产生的经验数据库可以进行输出。自适应加工技术广泛应用于叶盘、叶轮、叶片、机匣、辐板、飞机结构件、复合材料及飞机部装零部件等的自适应制造及维修,在设备支持上支持铣削、磨削、激光熔覆、激光打孔、机器人打磨、等离子处理和增材等应用。
2.1 自适应加工技术路线
针对涡轮工作叶片叶尖修复工艺的难点,即:每片修复的叶片的变形不一致,装夹的位置、角向不同,原有精铸精度的问题,诸如以上的实际问题都可以通过自适应加工技术快速地在线检测每一件待加工零件或部位,了解实际形状及位置分布,然后系统通过测量的数据,重新构造与设计相符的目标数模,生成唯一的个性化路径轨迹以满足产品制造,最终与设计、实物相符。自适应加工技术路线如图4所示。 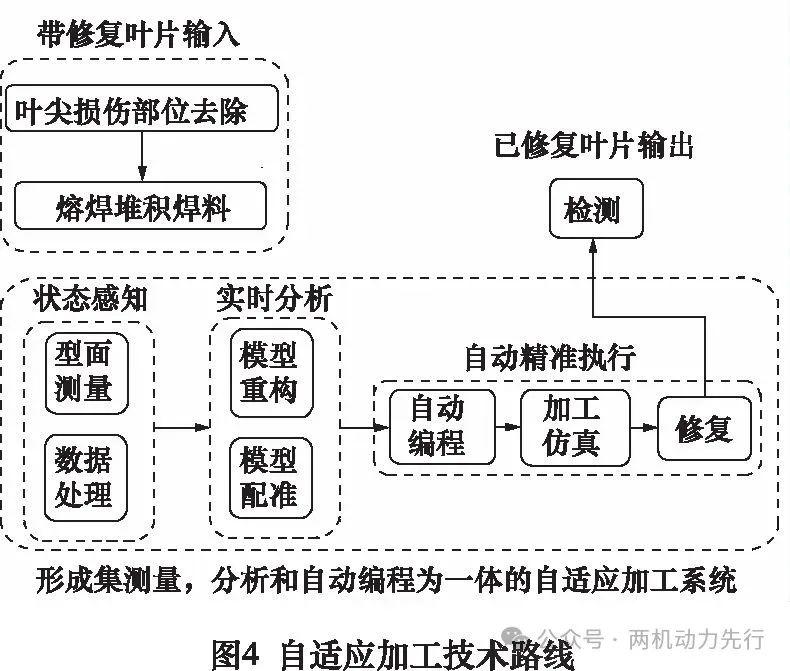
2.2 CAD模型数据配准技术
由于被加工对象毛坯个性化特征,重构出的CAD模型缺乏规则的基准平面找到其坐标系统,需要采用配准技术找正其坐标系统。空间两点集即理论模型X{xi}和被加工对象测量信息P{pi},将P点集经过旋转和平移使其与X点集的距离最小,建立测量信息P{pi}和理论模型信息X{xi}之间的空间变换关系,所述空间变换关系包括旋转矩阵R和平移矩阵T 。再采用最近点配对的方法,将P中每一个点,都在X中寻找一个与其距离最近的点配对,形成新的点集X’,如图5所示。 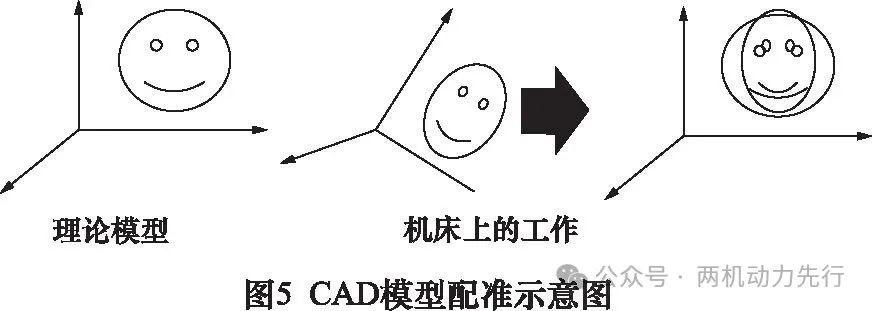
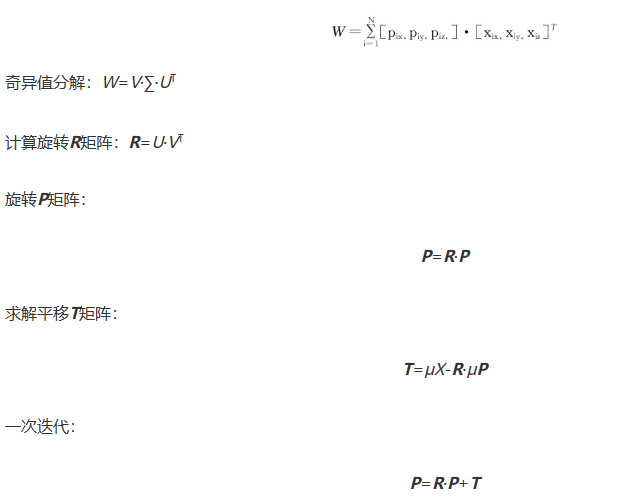
3 叶片叶尖损伤修复自适应加工技术验证
自适应加工系统包括自适应加工软件和机床、刀具等硬件系统,二者的集成是最终实现自适应加工的关键。在某型号高压涡轮工作叶片修理工作中,采用自适应加工系统开展叶片的修复加工,并完成多台发动机叶片的修复加工与应用验证。
3.1 试验步骤
步骤1:待修复叶片叶尖损伤区域经过融覆、堆焊方式填充后,通过在机检测获取叶尖损伤邻近区域的测量信息。 步骤3:用数据配准建立测量信息和理论模型信息之间的空间变换关系(空间变换关系包括旋转和平移),得出旋转和平移修正量,即最佳拟合后的旋转和平移量。 步骤4:依据理论模型信息生成加工刀位轨迹CLSF文件, CLSF文件中的理论刀位点、理论刀轴矢量,根据步骤3得出的在XYZ方向修正量,生成修正后的刀位点和刀轴矢量。 步骤5:利用修正后的刀轨,进行涡轮叶片叶尖损伤区域的磨削、抛光加工,从而实现精密叶尖的完整修复。 如图6所示,采用RMP40测头,φ6 mm测球在线检测,在叶尖邻近的2条截面各优化获得12个测量点,产生的测量数据文件可以反传回电脑软件系统,并依据测量数据在UG中自动生成加工模型。 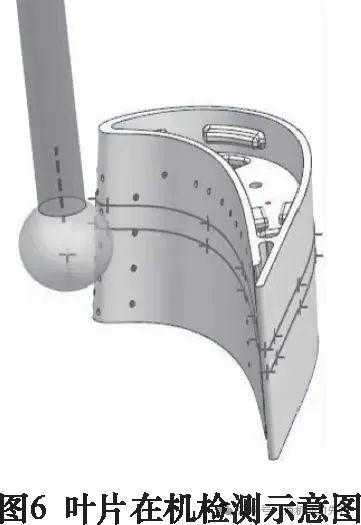
试验采用三轴立式加工中心,叶片通过快换工装托盘垂直悬臂安装于工作台,便于后续过程中机加工与特征加工重复装夹精度。如图7所示。
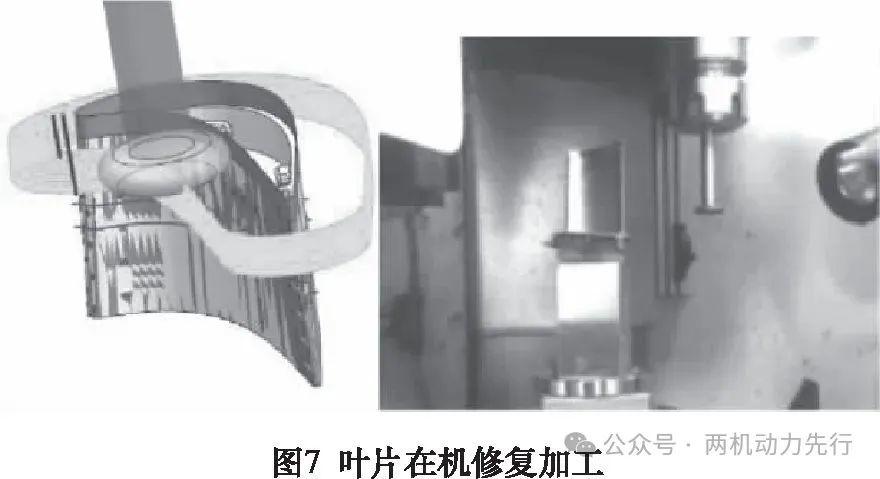
生成的加工刀位轨迹CLSF文件如图8所示。
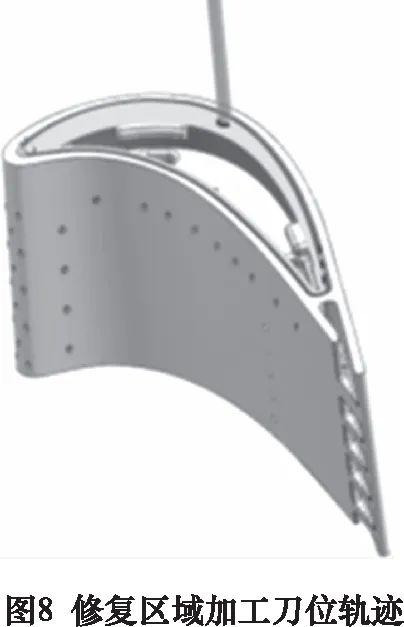
3.2 内腔及气膜孔保护
试验过程中,对于内腔及气膜孔不允许残留切屑及其他杂质的技术要求,工艺试验过程中对叶片内腔及多排气膜孔进行了保护。本次技术研究采用的是功能胶,将内腔及气膜孔密封,达到了孔的保护作用。据了解,国外此类叶片修复时,空腔及气膜孔保护,采用一种液体状的“多功能环氧树脂油灰胶”,冷却后凝固,达到保护作用。对其加热至100 ℃以上即溶化,变成“灰”,可吹掉,也可采用超声波清洗去除掉,小孔内也无残留。在后续批量工程化应用中,空腔及小孔的保护、清理将尤为重要,需继续寻找更适当的方式防止切屑及杂质的进入。
3.3 试验结果
通过对修复后的涡轮工作叶片叶尖型面进行测量,如图9所示,形状符合工艺技术要求。从外观检查可以看到,叶片修复区域与原有型面经自适应抛光后转接光滑过渡,如图10所示。内外腔的壁厚合格,表面粗糙度达Ra0.8 μm以下,其他技术指标均达到了工艺要求。通过荧光检查,机加的过程并没有造成新的裂纹等缺陷。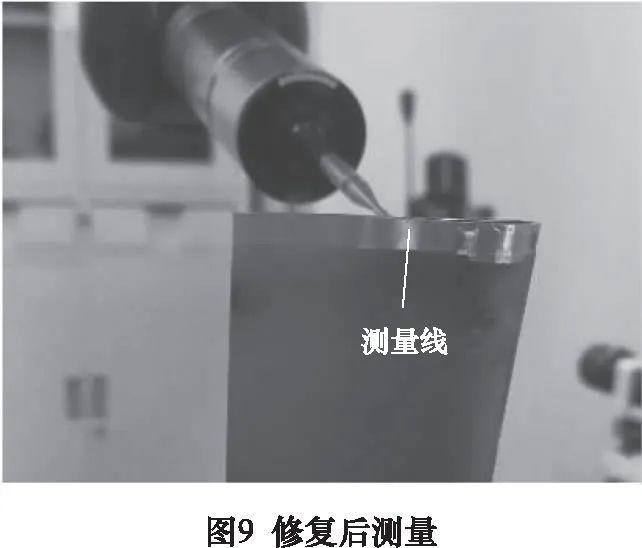
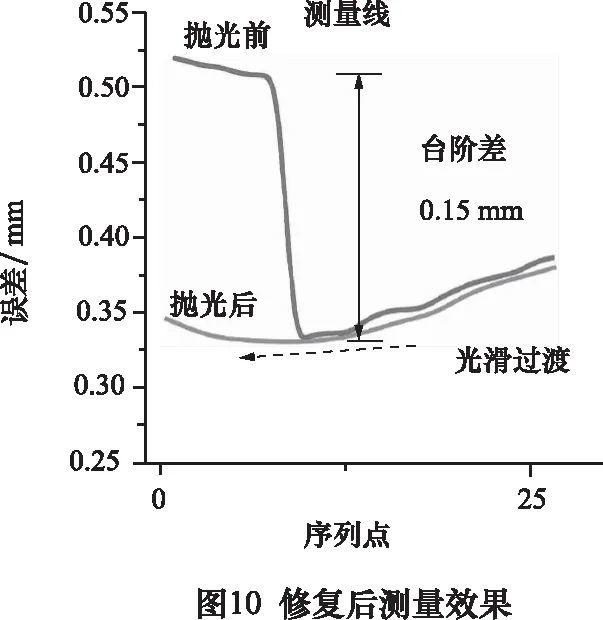
4 结语
本次涡轮工作叶片叶尖损伤修复技术研究与应用,提供现有设备单机的解决方案及工艺流程,自适应功能得到完整的应用与验证,实现叶型与前、后缘的平滑转接,确保品质的稳定,无需复杂的曲面重构,大幅度提高数据处理效率,可用于现场实时修复,单片叶片修复时间小于0.5h,快速实现低成本的再生制造,延长涡轮叶片的使用寿命。 未来将会有大批量航空发动机叶片的修复需求,叶片故障区域结构也会更加复杂,快速实现低成本的再生制造,需要跨越数字化、自动化和智能化3个台阶,要建立叶片修复与再制造智能化生产线及全流程技术体系。叶片修复技术也需要多专业的融合,如叶片缺陷智能识别技术,线激光高效在线测量技术,激光熔覆(焊)与机加复合机床研制与应用技术,增材制造技术等,使叶片修复系统具有自适应、自修复的高效率修理能力。
免责声明: 本文来源于《制造技术与机床》作者吴志新等