全极耳方形卷绕电池生产过程一致性分析
锂离子电池通常在组成动力电池组时需要将多个单体电池进行串联或者并联才能达到实际性能需求,并且随着单体电池数量的增加,使得电池一致性问题尤为突出。一致性问题引起电池使用寿命缩短、电池组性能和安全性降低等一系列问题。单体电池的不一致性主要来源于制造或存储过程和使用过程。生产过程中经常通过对制造工艺精度的控制来间接缩小不一致性,但这只能减小初始参数差异,也不能彻底消除。电池的一致性具有传递性和累积性,受众多因素交互影响,使用过程中初始参数的细微差别会被无限放大。我们可以从电池生产环节、电池分选、电池均衡、动力电池热管理等方面联合入手,改善这种情形。本文分享全极耳卷绕式方形锂离子动力电池生产过程的检测数据,并分析一致性。
电池具体的设计和生产过程为:电池正极材料采用三元体系,负极采用人造石墨,电池以卷绕方式组装,铝壳外包装。极片及卷芯和电池组装工艺过程如图1所示。全极耳电池卷绕时,极片和隔膜的布置方式如图1所示,正极极片在涂敷正极材料(30)时一侧边缘不涂布的侧面(15)和负极极片涂覆负极材料(40)时留白的一侧面(14)都作为极耳分别焊接在正、负极导流体上,正负极极片之间通过隔膜(170)隔离开,卷芯两侧分别漏出正、负极集流体,直接通过集流体与电池正负极连接。从极耳角度提高了电池功率特性,这样电流流经的距离短,在大倍率下电流密度分布均匀,可以实现高功率密度,极片发热量也小。组装好顶盖后,利用激光焊接或电阻焊的方式将正极留白集流体与正极汇流排焊接在一起,将负极留白集流体与负极汇流排焊接在一起,当设计容量比较大时,可以两个卷芯并联在一起。焊接时,可以先将多只卷芯并联在一起焊接;或者每个卷芯分别焊接,在激光焊接之后将多只卷芯并联在一起。采用绝缘膜包覆焊接极耳的卷芯,然后拆入壳体内,采用激光方式将顶盖和壳体焊接在一起。电池干燥之后进行注液和预充化成,将开口化成后的电池注液口封好胶钉,覆盖铝质注液栓,之后将注液栓焊接在电池顶盖上进行封口,使电芯内部完全被密封起来。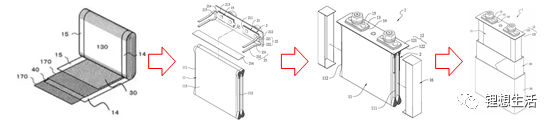
正、负极极片涂布均采用狭缝挤压式涂布技术,使用液压伺服轧机的恒辊缝模式辊压。极片涂布和辊压过程中,将长度约500 m的极片收成一卷,并作为一个批次做首尾检测,取样器裁切φ60mm的圆片样品,称量极片重量和厚度,计算极片的面密度、压实密度,每个批次取样3个测试和计算数据。正极极片各批次测试数据如图2-图3所示,极片两面面密度平均值为36.89 mg/cm2,涂布稳定性较好。极片辊压通过控制极片厚度确定涂层压实密度,正极极片辊压之后,正极压实密度控制在3.00 g/cm3,极片辊压厚度波动小,稳定性比较好。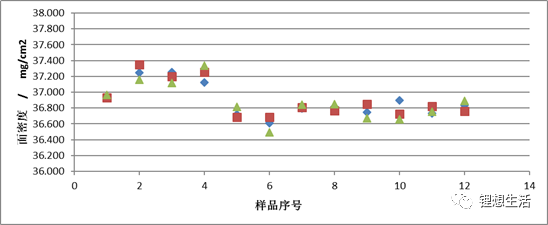
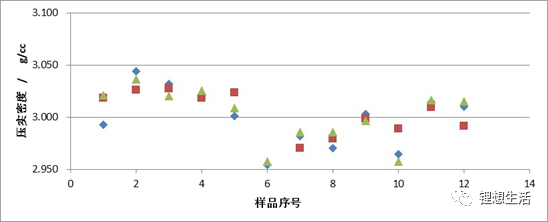
负极极片各批次测试数据如图4-图5所示,极片两面面密度平均值为16.13mg/cm2,涂布稳定性较好。极片辊压通过控制极片厚度确定涂层压实密度,负极极片辊压之后,压实密度控制在1.62 g/cm3,极片辊压厚度波动小,稳定性比较好。最后,正负极极片的面密度和压实密度的范围、平均值和标准偏差汇总在表1。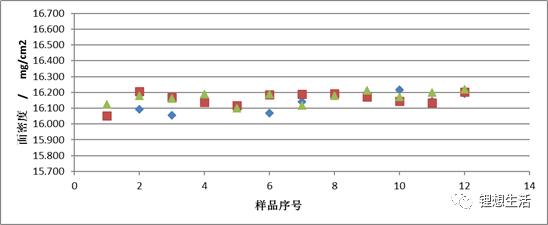
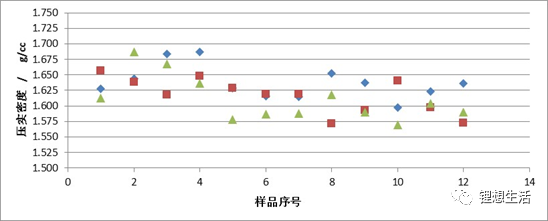
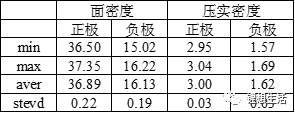
卷绕后,卷芯需要大量的检测,确保产品质量,主要包括:(1)电芯外形尺寸,包括高度,宽度,厚度,胶带宽度和位置,留白集流体整齐度等。这些尺寸可以直接测量,和卷绕工艺以及设备精度相关。(3)极片宽度,在宽度方向负极也需要超出正极一定余量,隔膜超出负极一定余量。宽度方向的对齐度直接由卷绕工艺精度决定,精度高时,余量尺寸可以更小,电池能量密度更高。但是,电池安全性系数降低,必须确保工艺精度,否则对电池存在巨大安全隐患。卷芯每层极片的对齐度一般采用X-射线全部检测卷芯四个边角,当正负极之间的宽度相对尺寸不满足要求时设备自动报警剔除不良品。(5)极片切断毛刺,极片切刀长期使用会出现磨损,影响切断效果,因此切刀需要进行寿命管理,定期检测切断质量,避免毛刺。一般切断毛刺观察过程为:取切断极片,在光学显微镜下观察切断面,检测是否存在毛刺。关于毛刺的管控标准,一般毛刺尺寸小于隔膜厚度的一半,但是有些厂家控制要求更加严格,毛刺不超出涂层;(6)卷芯内部其它缺陷,如极片弯折、涂层阴阳面、异物等。选择卷芯的质量进行分析,数据直方图如图6所示,直方图通过收集到的卷芯数据进行处理,来反映产品质量的分布情况,判断和预测产品质量及不合格率。在统计数据时,我们把数据按照不同的范围分成几个组,分成的组的个数称为组数。卷芯质量分布基本符合正态分布,平均质量为179.86g。质量范围177.955~178.155g内的卷芯数量偏多,偏离正态分布。极片在加工过程中,对于单面涂层、漏箔等缺陷极片会做出标记,在卷绕时单极片卷曲扔出。但是,仍旧常常出现缺陷极片出现在卷芯中,对卷芯作质量检测,剔除质量不合格品,能够进一步确保品质。质量检测异常主要的原因还是极片加工过程产生的不良品,比如涂布面密度不满足要求,单面涂层,极片存在胶带等缺陷。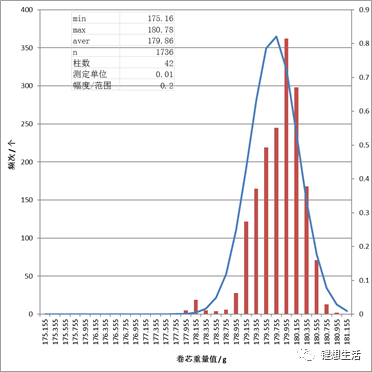
部分卷芯拆开破坏性测试,主要分析正负极和隔膜的长度数据,具体结果如图7所示,正极长度约2.20m,负极长度约2.37m。为了正极扩散过来的锂离子在负极有对应接纳嵌入晶格,负极必须全部包裹正极,并有一定尺寸余量。同时为了避免短路,隔膜必须包裹负极。卷绕电芯在长度方向必须保证负极与正极相比具有余量,隔膜也要包裹负极。极片相对位置非常关键,具体参数包括隔膜长度,以及与负极的相对尺寸,正负极之间的相对位置等。这些尺寸受到极片涂布规格、卷绕工艺等影响。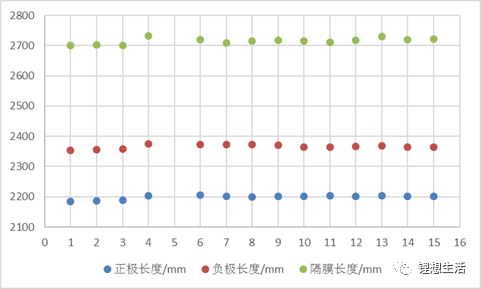
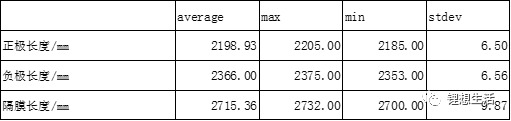
电池组装完成后,充放电测试电池的容量、直流内阻等参数。容量分布时电池所有工艺影响因素的累积,通过这个参数可以分析电池的一致性,综合了所有工艺的误差。电池容量分布如图8和表2所示。工序能力是工序在稳定状态时所具有的保证产品质量的能力。受工序中的操作人员、机器设备、原材料、工艺方法、工作地环境等因素综合影响和制约。表现在产品质量是否稳定、产品质量精度是否足够两方面。如图9所示,最后以电池容量数据以依据,综合分析电池生产的工序能力CP=1.085,电池生产能力满足要求。1. Cp>1.33 。当Cp>1.33时表明工序能力充分,这时就需要控制工序的稳定性,以保持工序能力不发生显著变化。如果认为工序能力过大时,应对标准要求和工艺条件加以分析,一方面可以降低要求,以避免设备精度的浪费,另一方面也可以考虑修订标准,提高产品质量水平。2. 1.0<cp≤1.33。当工序能力指数处于1.0~1.33之间时,表明工序能力满足要求,但不充分。当cp值很接近1时,则有产生超差的危险,应采取措施加强对工序的控制。< span=""></cp≤1.33。当工序能力指数处于1.0~1.33之间时,表明工序能力满足要求,但不充分。当cp值很接近1时,则有产生超差的危险,应采取措施加强对工序的控制。<>3. 0.67<cp≤1.0。当工序能力指数处于0.67~1.0时,表明工序能力不足,不能满足标准的需要,应采取改进措施,改变工艺条件,修订标准或严格进行全数检查等。< span=""></cp≤1.0。当工序能力指数处于0.67~1.0时,表明工序能力不足,不能满足标准的需要,应采取改进措施,改变工艺条件,修订标准或严格进行全数检查等。<>4.Cp≤0.67。当工序能力指数小于0.67,表明工序能力严重不足,必要时要停工整顿。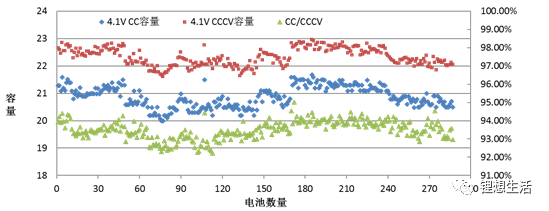
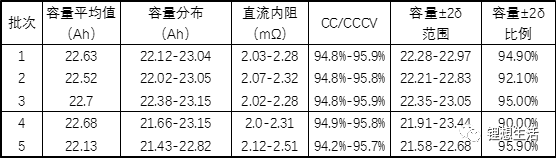
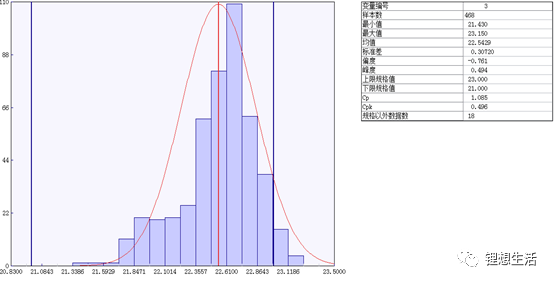
著作权归作者所有,欢迎分享,未经许可,不得转载
首次发布时间:2023-09-21
最近编辑:7月前