纯电动汽车电驱动总成NVH分析与实例解析
随着纯电动汽车产业的发展,电驱动总成的集成程度越来越高, 国内零部件厂商的“二合一”“三合一”“六合一”的驱动系统 总成都陆续面世。在给整车客户带来快速方便的动力匹配的同时,电驱动系统一直 存在的问题及产生的原因也越来越复杂,这其中就包括动力总成 的NVH、效率及综合耐久性问题等。纯电动汽车电驱动总成通常由电机和减速器组成,多采用永磁同 步电机加两级减速器的组合形式。电驱动总成存在啸叫的原因复杂,主要包括:电机电磁激励、减 速器系统共振和电驱动总成系统耦合模态共振等。结合某型号电驱动总成在整车试验过程中,客户发现存在结构共 振问题,本文主要通过MASTA软件分析,对动力总成进行仿真 分析,找出动力总成出现结构共振的原因,并加以修正。在整车搭载NVH测试过程中,可通过LMS数据采集前端采集车 内近场噪声数据,将采集到的数据通过LMS Test.Lab数据分析软 件对近场噪声进行噪声阶次分析,找出发生啸叫的对应阶次,再 通过啸叫噪声阶次分析,判断啸叫噪声的激励源。本文针对的某型号电驱动总成整车搭载NVH测试客户反馈的试 验数据如图1所示。经客户反馈,在整车WOT工况下,输入端转速在1 600~2 000 r/min(586.6~ 733.3 Hz)之 间 时,电驱动总成第22阶存在 共振啸叫问题,根据电驱动总成的结构,基本可以确定是驱动总 成中的减速器高速级产生的噪声。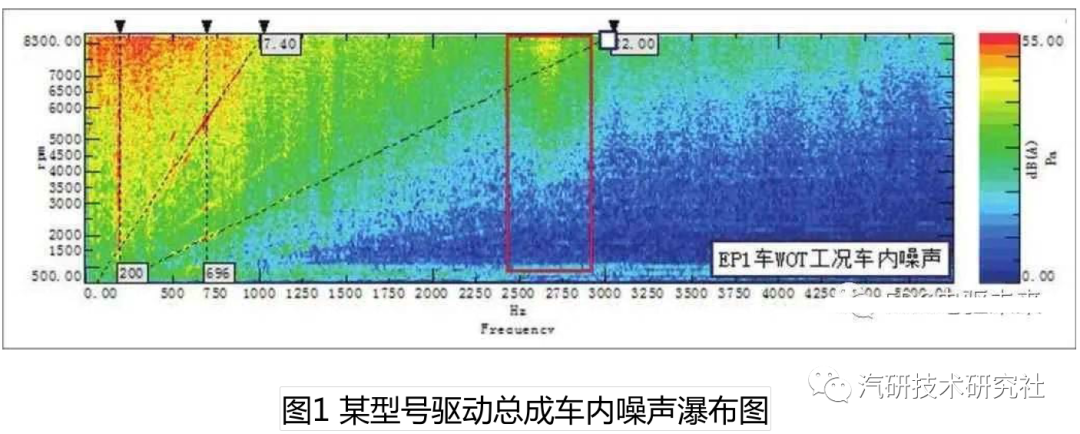
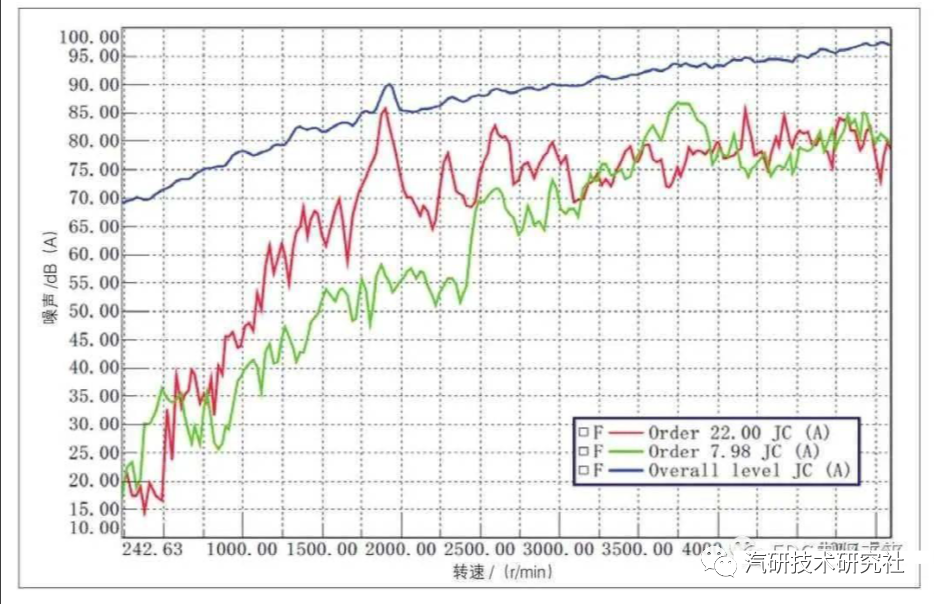
图2 第22阶阶次噪声图
由图2可知,总成第22阶噪声在2 000 r/min左右存在明显突变;由图1可以看出,总成除第22阶外,在696 Hz附近其他阶次噪声 的系统共振响应明显,由此判断,总成在696 Hz附近,存在有系 统结构共振,需要调整系统结构来改善这一情况。根据电驱动总成产品建立MASTA分析模型,如图3所示。电驱动总成齿轮参数见表1。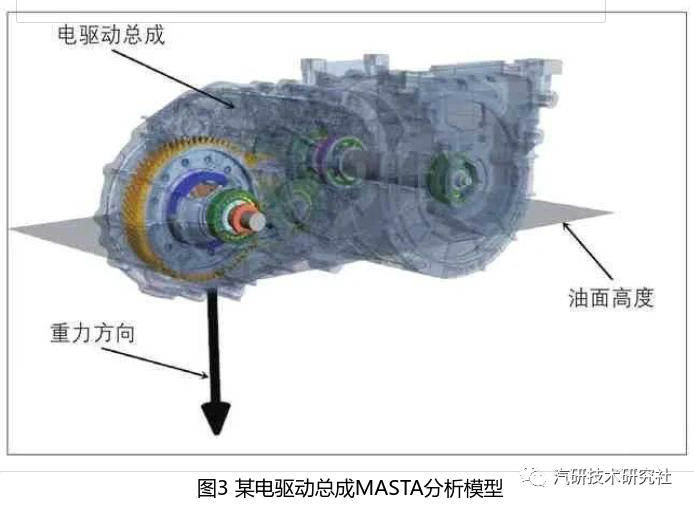
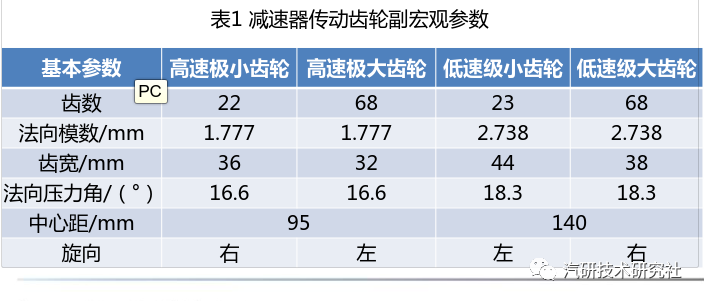
在软件中输入齿轮副的宏观参数及微观修形后,通过MASTA软件 仿真,得到该电驱动总成高速级齿轮副在整车WOT工况下的传递 误差,如图4所示。在整车WOT工况下,高速级齿轮副传递误差的峰值计算结果是满 足设计要求的,且传递误差的频域幅值也不大,说明驱动总成第 22阶的阶次激励其实并不算大,产生啸叫问题的原因应该是存在 系统共振。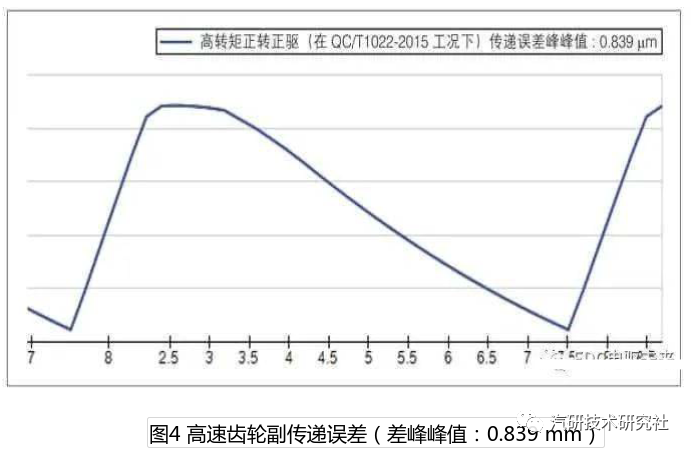
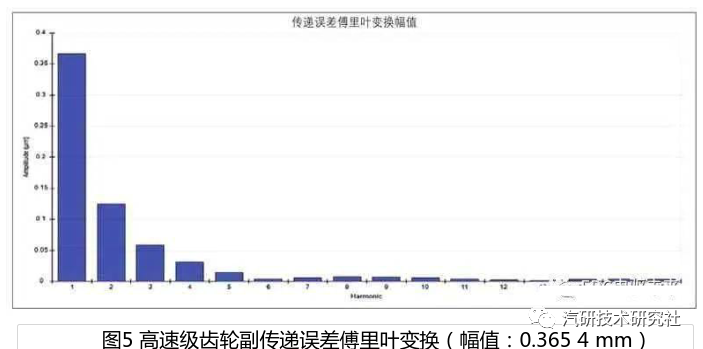
在1000~2000 r/min范围内,第22阶激励与系统固有频率存在多 个潜在共振点。其中,系统耦合模态的第13阶(651.1 Hz)在本次啸叫范围内, 可确定为问题频率。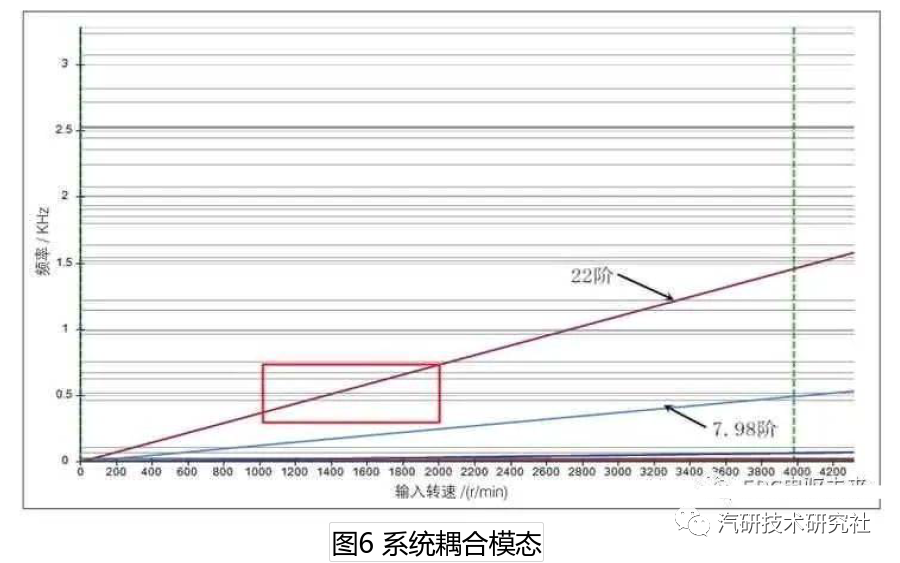
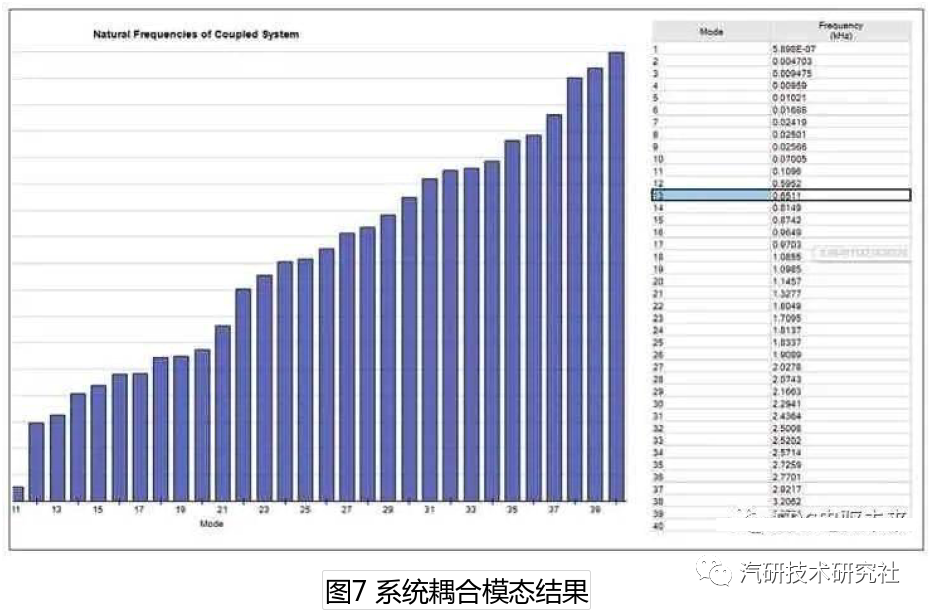
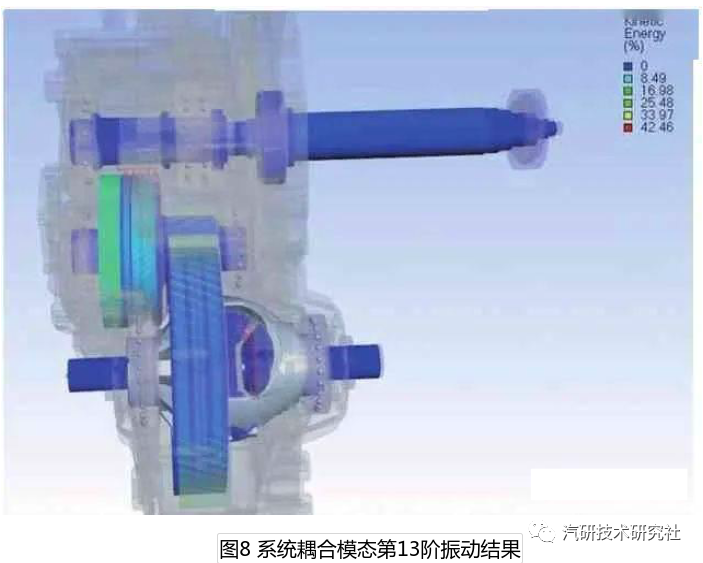
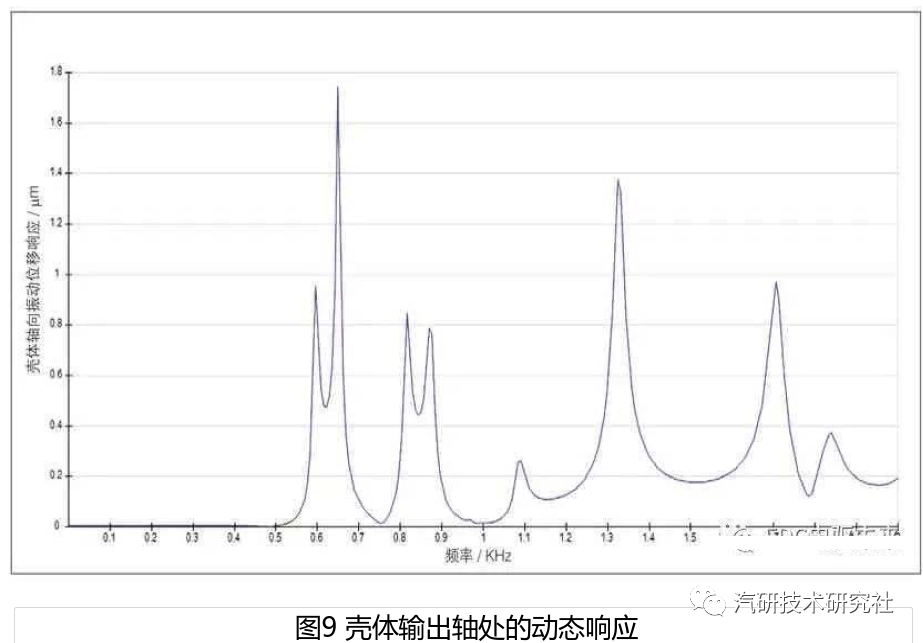
由图9可知,在651.1 Hz时壳体在输出端前轴承处的动态响应幅值针对以上情况,考虑增加高速级大齿轮腹板厚度,分别取增厚5 mm和10 mm进行仿真对比,主要分析壳体在输出端轴承座处的 动态响应,结果见表2。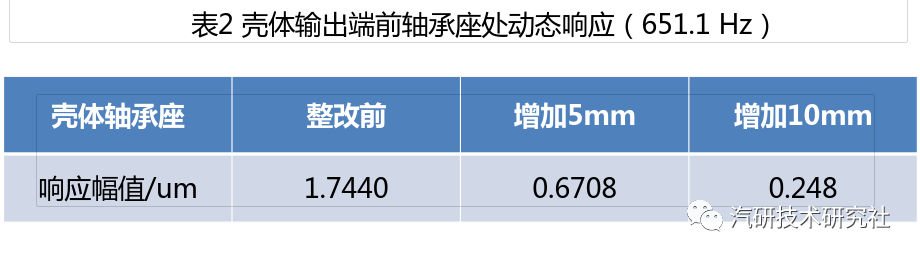
结合数据进行分析,可知增加高速级大齿轮腹板厚度之后,系统 的刚度会有明显的改善,在651.1 Hz频率上,壳体在输出端前轴 承处的动态响应有明显的改善。其中,腹板厚度增加5 mm,壳体在输出端前轴承处的动态响应 由1.744 μm下降到0.670 8 mm,在整车试验标准中已经达到标 准要求。考虑到整车对于电驱动总成NVH性能的要求及总成零部件的制造 成本,确定将高速级大齿轮腹板厚度增加5 mm。为验证上述产品优化结果及软件分析结果的正确性,我们将优化 后的总成产品进行装车测试,并将测试结果与优化前的测试结果 进行对比。在整车WOT工况下,主观测试优化后的减速器装车噪声试验效 果明显要优于优化前。通过客户LMS数据采集前端采集车内近场噪声数据,将采集到的 数据通过LMS Test.Lab数据分析软件对近场噪声进行噪声阶次通过验证可知,2000~4000 r/min转速范围内,振动降低明显, 与车内噪声趋势一致,4 000 r/min以上,因试验车辆转速上升 速率不一致,故不做对比。整车起步到2 000 r/min区间内,改善效果并不明显。从客户两次测试的对比数据中并未发现第22阶噪声曲线图在650 Hz左右存在结构共振,但是从车内噪声主观评价上来说,1600 ~ 2 000 r/min转速范围内的啸叫问题确有改善。本文通过我公司某个电驱动总成项目客户反馈存在NVH啸叫问 题,利用MASTA软件对电驱动系统总成进行有限元计算分析, 并找到对应的解决方案。该方案虽然解决了客户提出的阶次噪声超标的问题,但是并没有 很好地解决低频啸叫的问题,试验方法和分析方法仍需要进一步 优化。我们仍然可以得到以下结论,供同领域的研究人员参考:1)电驱动总成因集成度高,使得系统的耦合模态发生改变,使 总成NVH问题变得更加复杂。2)总成某个零部件的调整会影响整个系统的耦合模态。3)可通过提高某些零部件的刚度来降低系统的动态响应,解决 部分因传递路径而引起的NVH啸叫问题。4)调整系统刚度只是从噪声传递路径上减小NVH啸叫问题,传 递误差才是解决NVH问题的关键,降低齿轮副工作过程中的传 递误差才能够减小振动激励源,从根本上解决NVH啸叫问题。著作权归作者所有,欢迎分享,未经许可,不得转载
首次发布时间:2023-11-16
最近编辑:1年前