Simerics | 润滑系统三维瞬态CFD模拟
随着数值分析技术的进步以及空化与气蚀模型的完善,内燃机润滑系统CFD仿真在内燃机润滑系统设计与开发中发挥的作用越来越大。 传统的分析方法,对于润滑系统的系统级仿真通常采用一维流动模型。轴承模型基于实验数据或其它数据的零维表达,因此,需要引入经验公式。而这种零维处理是不合理的,因为泵出口和曲轴箱之间的绝大多数压降发生在轴承上。对于润滑系统部件级的仿真分析,由于部件(如容积泵、轴承等)几何结构复杂,具有双曲线连续表面且空隙小,在传统的分析方法中也常采用零维和一维模型来进行仿真。流体机械和系统虚拟仿真软件Simerics-MP/MP+致力于解决此类问题的三维CFD仿真,其它类型组件的三维CFD仿真也越来越多地应用于产品开发中。通过Simerics-MP/MP+软件对16缸往复式内燃机润滑系统进行仿真,计算域见图1。
模型组件包括:
机油齿轮泵及相关的压力调节阀(以及所有先导管路连接);
9个(曲轴)主轴承(MB);
16个连杆轴承(RB);
16个活塞销;
7个凸轮轴轴承(CB);
16个活塞冷却喷嘴;
32个气门挺杆;
机油冷却器及滤油器。
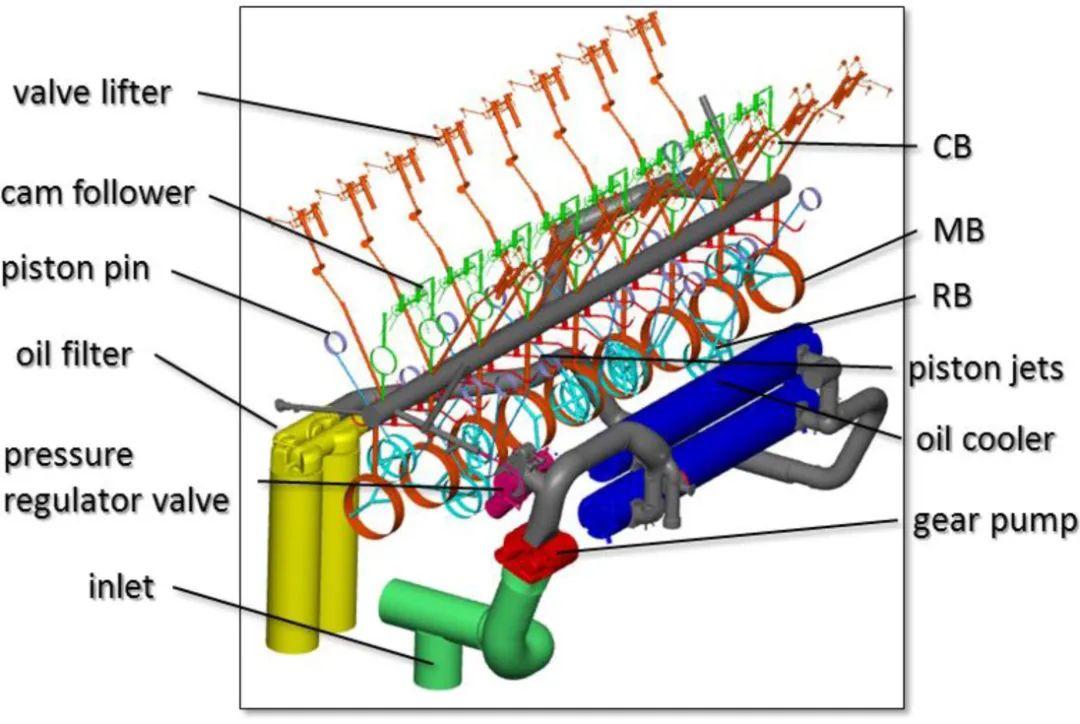
Simerics-MP/MP+建立的三维CFD模型给出了发动机润滑系统建模的一个重大进展,不仅可以对组件及组件之间的相互作用进行CFD分析,而且有利于发动机性能优化、节约开发时间和开发成本。轴承模型是三维CFD模型,直接求解完整的Navier-Stokes方程(质量、动量和能量),不用简化为雷诺方程来求解。轴承内轴颈的轨道轨迹以及由于燃烧和其它载荷引起的轴承变形被输入到模型中。泄漏通过微米级,动态间隙严格建模。间隙使用结构化网格进行网格划分,再通过使用交互面接口(MGI)连接到网格的其余部分。通过将流动方程与柱塞上的力平衡强耦合,预测压力调节阀的脉动运动。通过轴承的流动特别复杂,受到几何、物理和数值的影响。
(a)主轴承和凸轮轴承内的轴颈组合轨道运动和旋转;
(b)连杆轴承和活塞销内的复杂轴颈运动;
(c)燃烧和其它载荷引起的轴承变形;
(d)轴承内微米级的泄露路径上有瞬态泄露流动。
(a)润滑油的气穴现象;
(b)不凝气体进出溶液;
(c)曲轴箱气体回流到轴承间隙;
(d)低温下的非牛顿性考虑。
3 从数值角度来看,CFD模型应满足工业产品开发的要求:
(a)质量良好的瞬态、移动、变形网格;
(b)提供可接受的工程精度预测,至少应给出不同设计间的区别;
(c)在合理的运行时间内产生收敛解;
(d)以稳健的方式进行上述操作,模拟不会发散或崩溃。
上面列出的每一项本身都是一个挑战。
因此,轴承流动固有的复杂性表明轴承三维处理的重要性。通过高度自适应的二叉树笛卡尔网格技术,自动生成高质量的、瞬态的、移动的、变形的六面体细胞网格。高度自适应的二叉树笛卡尔网格技术:
Simerics-MP/MP+自带自动化笛卡尔网格生成器,采用专有的几何等角自适应二元树算法,既CAB算法,CAB算法在由封闭表面构成的体域生成迪卡尔网格。在靠近几何边界,CAB自动调整网格来适应几何曲面和几何边界线。为适应关键性的几何特征,CAB通过不断的分裂网格来自动的调整网格大小,这也是利用最小网格分辨细节特征最有效的方法。 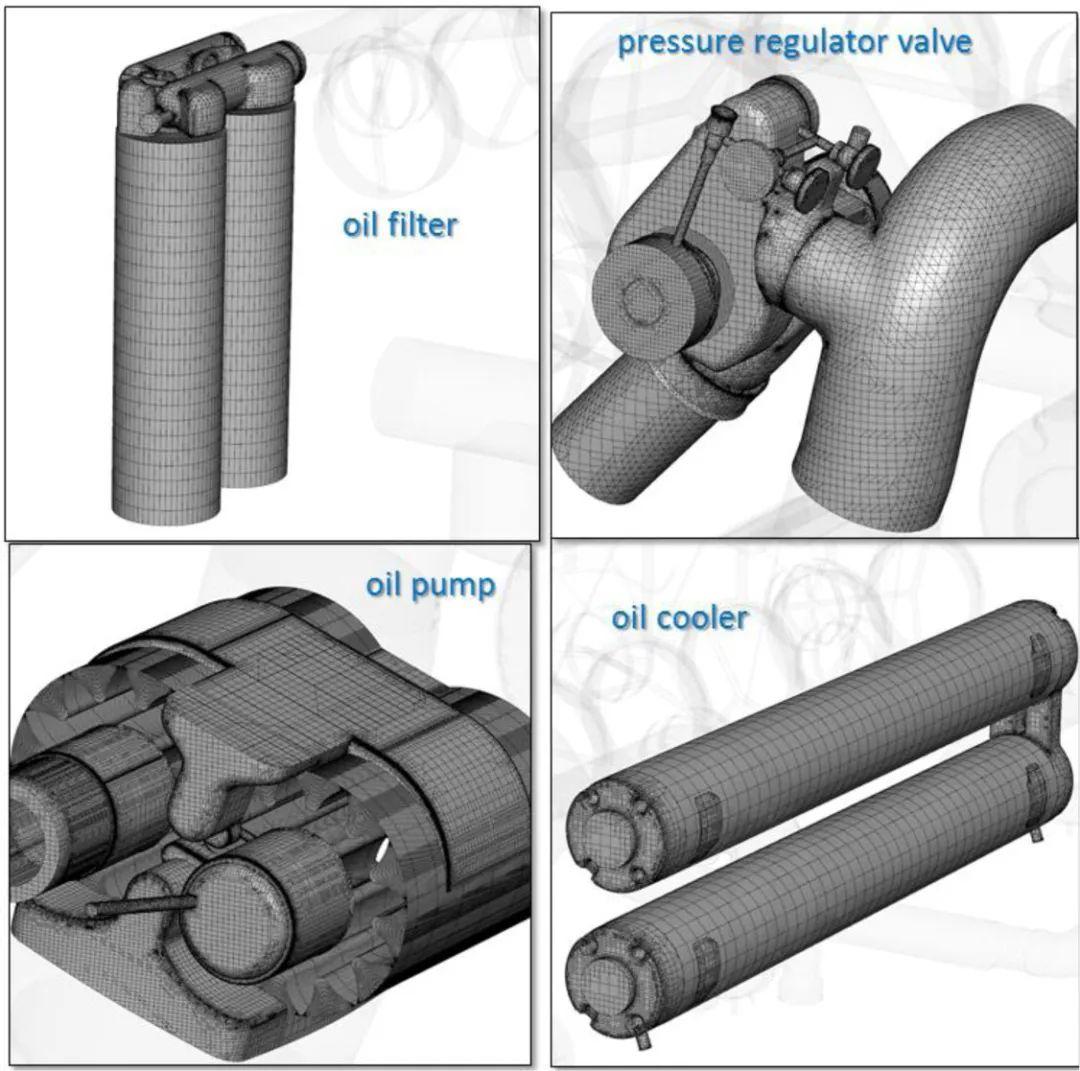
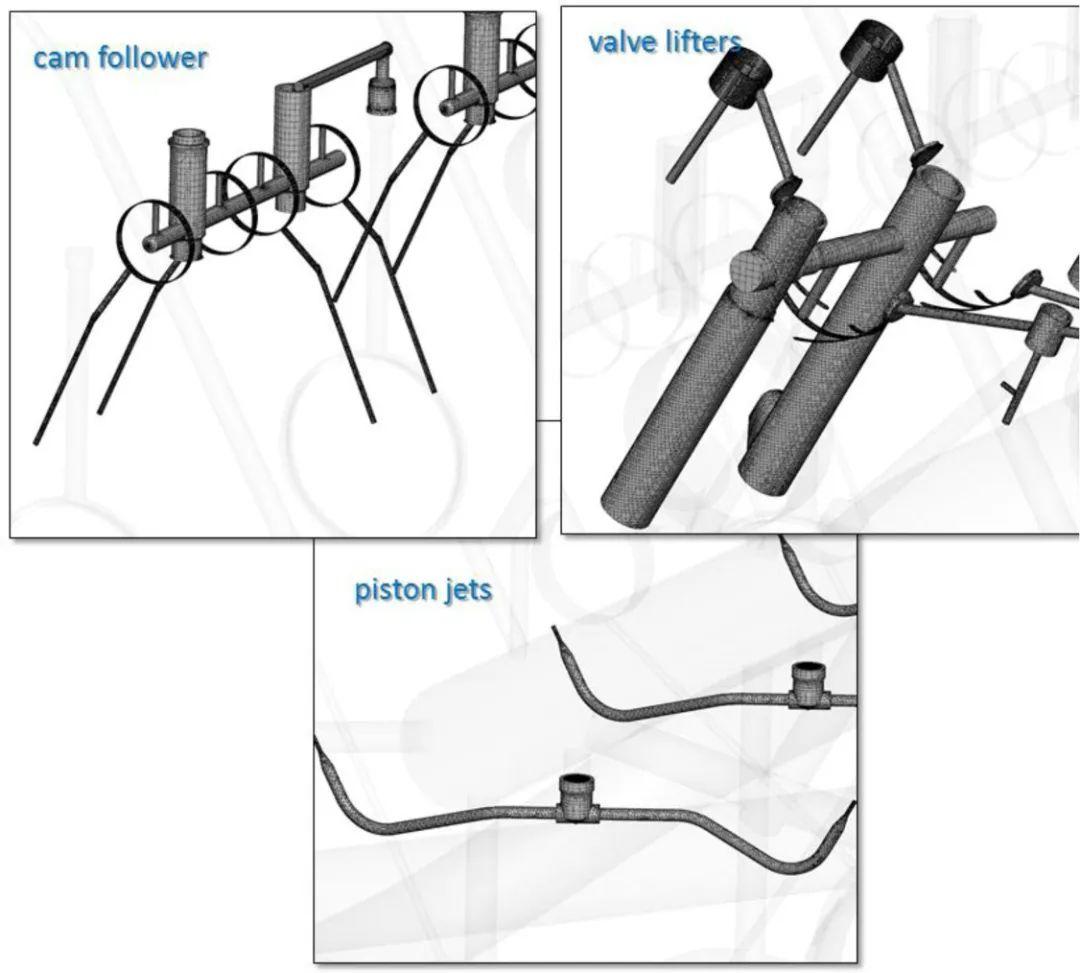
在额定发动机转速下,曲柄角旋转开始时系统中的压力分布如图4所示。
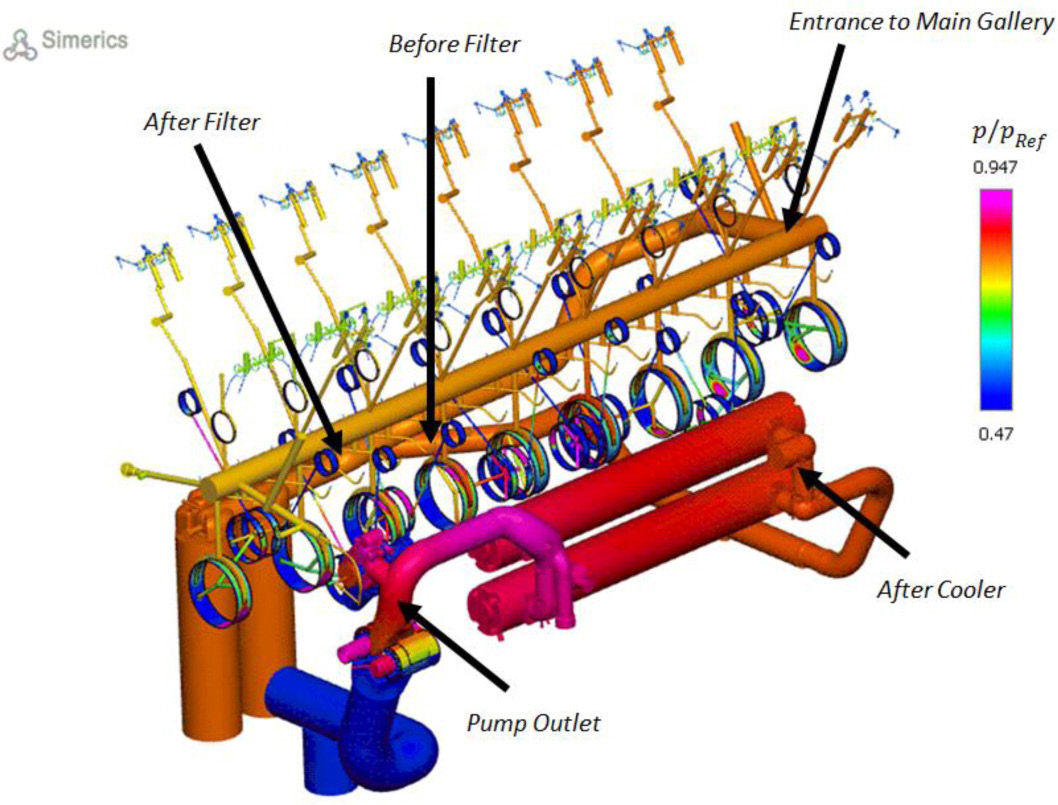
系统的峰值压力出现在泵的出口处,而泵的进气管道中的压力却接近于环境压力。峰值压力在整个系统中逐渐降低,在轴承和挺杆出口处达到环境值(轴承和挺杆出口是模型域的边界)。 在图4中还可以看到主轴承进给槽中的高压(红色)和轴承边缘沿轴向的低压(深蓝色)。因此,大部分压降发生在轴承只有几毫米宽的轴向流距离上。 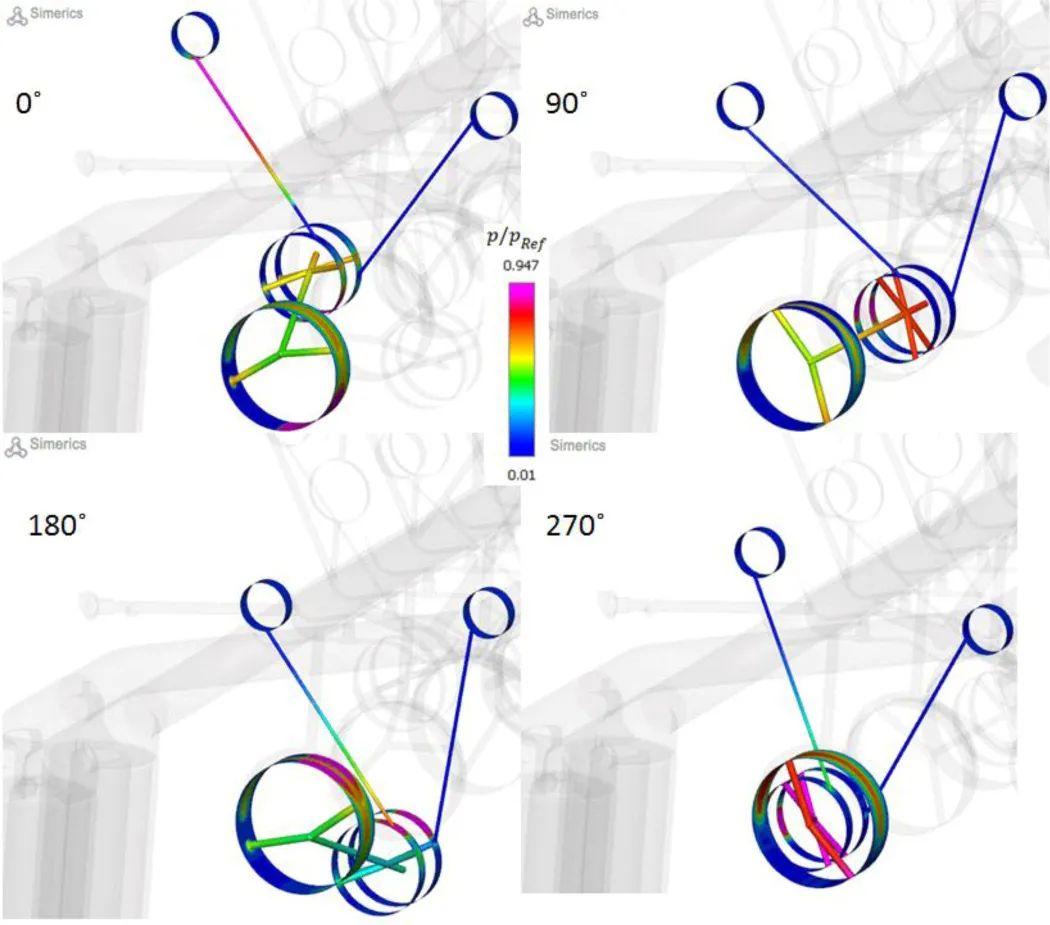
图5 四个瞬态下主轴承、连杆轴承和销轴承中的压力分布
图5显示了仿真过程中4个不同曲轴转角下主轴承、连杆轴承和销轴承中的压力细节图,可以看出,在不同时刻的轴承偏心率,以及十字钻不同的相对位置,压力差别也非常大。图6显示了额定发动机转速下轴承系统中总(蒸汽+空气)体积分数的分布。系统中观察到的曝气主要是由于曲轴箱空气回流到轴承中,以及在某些时刻的膜厚不均和高挤压速度导致的局部气体释放,而不是由空化产生。
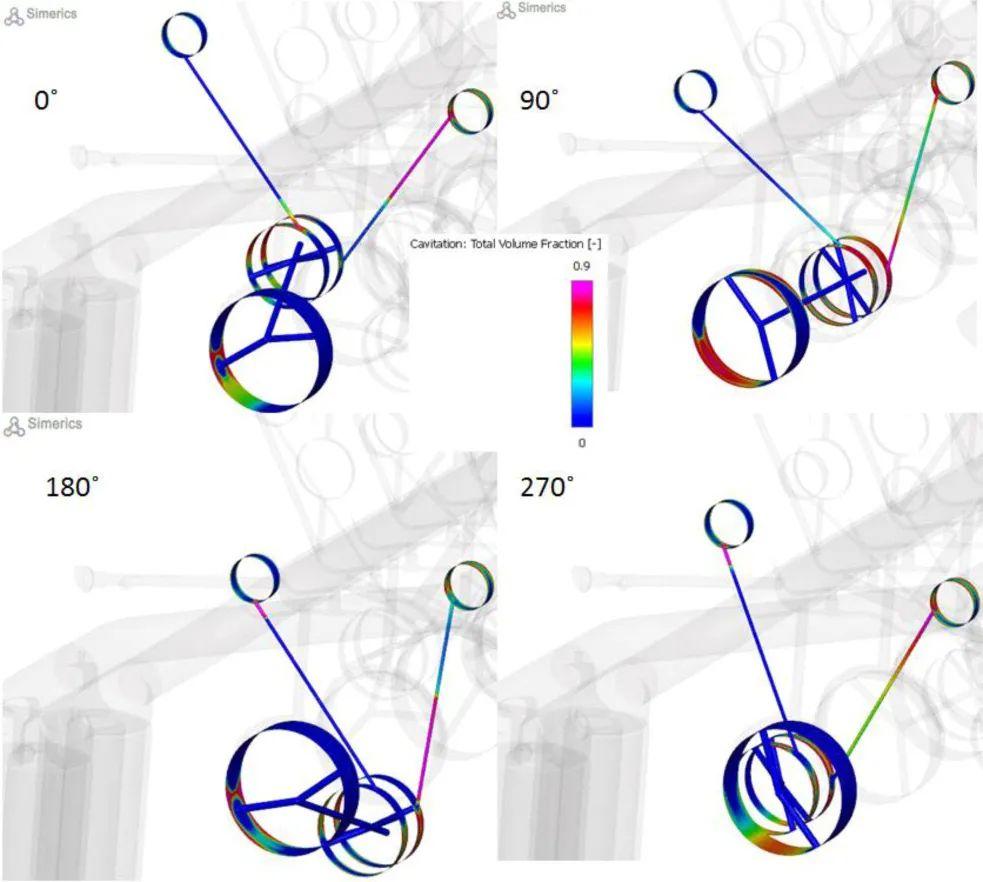
图7 瞬态下主轴承、连杆轴承和销轴承总体积分数分布
图7给出的是在4个曲柄角旋度下,主轴承,连杆轴承和活塞销轴承以及输油通道的总气体体积分数。曲柄角随时间变化的结果清楚地表明可以忽略空化效应。表2给出了在图4所示位置的所有运行条件下,润滑系统在不同位置的曲柄角时间平均标准化表压。相应的标准化测量压力与表3所示的模型预测非常吻合。表2 标准化表压(p/pRef )
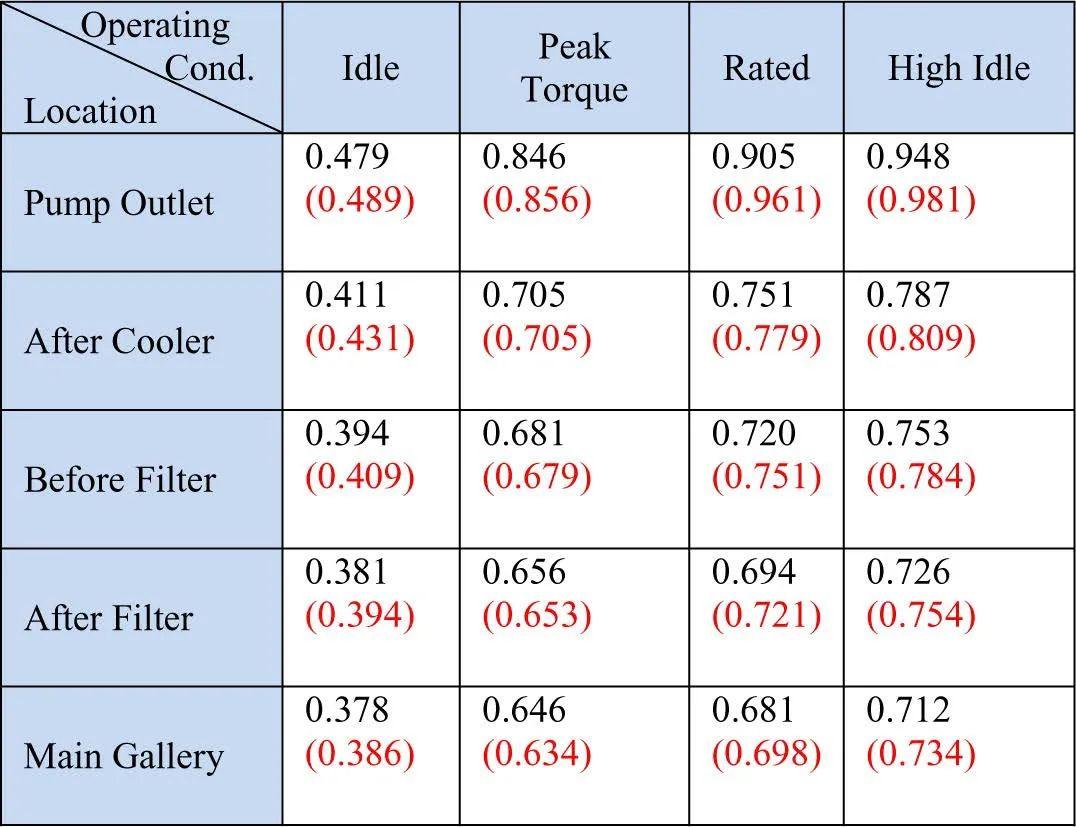
在怠速时,泵将机油压力从环境压力(p/pRef =0)升高到出口压力(p/pRef =0.479)。当油流过润滑系统时,主油道中的p/pRef =0.378将减少约20%,这主要是由于过滤器和冷却器中的压降导致。轴承、挺杆和冷却喷嘴的供给压力在该压力的几个百分点内。类比燃油系统,主油道起到“共轨”的作用,即几乎均匀的压力源(即沿主油道长度的压力变化不大,如图4所示将机油输送到润滑系统各个部件,如轴承、升降机、冷却喷嘴等。机油从主油道流过各种部件(如轴承和挺杆间隙)中狭窄的微米级通道,到达其最终目的地曲轴箱。其余80%的压降大部分发生在这些部件上。同样的,还可以得到在峰值扭矩、额定和高怠速条件下的分析结果。
所有工况下的预测压力和测量压力之间的百分比误差如表3所示,可以看出,在所有工况下两者都吻合得比较好,所有误差都在6%以内。表3 润滑系统不同位置压力模拟预测与实验测量的误差百分比
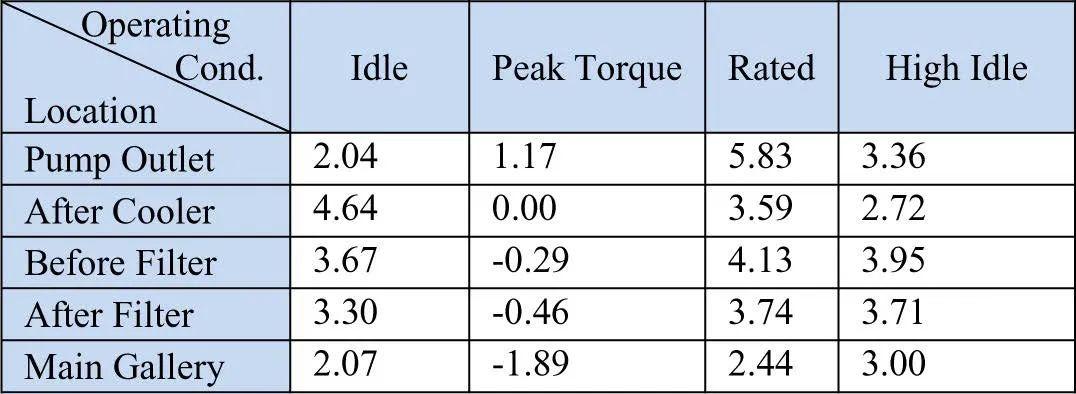
鉴于上述结果,应优先考虑在整个润滑系统模型中,流经轴承、挺杆等部件的流动达到最大精度,以便准确预测压力。同时,再次证实了获得正确轴承流动状况的重要性。因此,与采用近似处理的零维和一维模型相比,三维轴承模型的选用也更加重要。实际情况中,设备几何及轴承内的流动本质上是三维的,因此在不作任何假设的情况下求解流体流动的三维Navier-Stokes方程无疑是捕捉真实情况最精确的方法。特别是零维或一维方法将此类轴承简化为孔板或另一种流动阻力模型,使得模拟效果大打折扣。三维方法的优点是可以在模型中直接获取轴承间隙的精确几何,这也意味着不需要任何形式的简化。通过Simerics-MP/MP+对多缸发动机全润滑系统建立全面、瞬态、三维CFD模型,模型结果表明系统大部分压降和流率发生在轴承、挺杆和活塞冷却喷嘴中,从而证实了对这些部件进行三维分析的重要性。计算结果表明,因为压力调节阀控制主通道压力和润滑系统流率,因此对压力调节阀的流固耦合受力平衡进行正确的建模至关重要。
与当前主流的一维模型相比,Simerics-MP/MP+提供的三维CFD仿真分析是发动机润滑系统仿真分析的一个重大进展!